Materialversorgung: Technik, die sich bewährt hat
Dosier-, Misch- und Förderanlagen
Beim Bau einer neuen Produktionshalle setzte der Kunststoffverarbeiter C. Hübner GmbH aus dem bayerischen Marktoberdorf auf ein bewährtes Materialversorgungskonzept einschließlich zentraler Förderung von der Werner Koch Maschinentechnik GmbH.
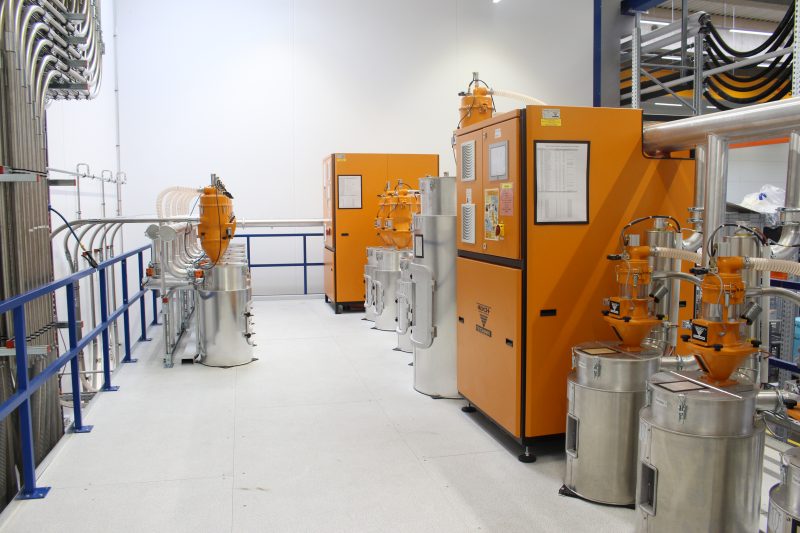
Die obere Bühnenetage bietet noch Ausbaureserven für zusätzliche Trocknungstrichter. Die beiden frenquenzgeregelten Trockenlufttrockner vom Typ »CKT« liefern 300 bzw. 500 Kubikmeter pro Stunde (Bild: Koch-Technik).
Die C. Hübner GmbH steht seit 1975 erfolgreich für die Bereiche Automotive, Sanitär sowie Konsumgüter. Aufgrund des stetigen Wachstums in den vergangenen Jahrzenten wuchs auch der Maschinenpark, wodurch die Firma platzmäßig an ihre Grenzen geriet. Für das circa 200 Mitarbeiterinnen und Mitarbeiter starke Unternehmen wurde daher ein Neubau geplant. Nach einer einjährigen Bauphase konnte im Oktober 2018 die neue, rund 5300 Quadratmeter große Produktionshalle in Marktoberdorf im Allgäu eingeweiht werden, die neben dem eigenen Werkzeugbau auch der Spritzgießfertigung dient. Insgesamt 22 Spritzgießmaschinen in Schließkraftbereichen von 35 bis 350 Tonnen beherbergt das Unternehmen in Marktoberdorf. Rund 25 Millionen kundenspezifische Spritzgussteile, die im 1K-, 2K- oder auch im 3K-Spritzgießverfahren gefertigt werden, verlassen jährlich die Produktionshalle. Zusätzlich findet auch eine neue zentrale Förderanlage hier ihren Platz. Das Unternehmen vertraut in diesem Punkt ganz auf die Werner Koch Maschinentechnik GmbH. »Die Technik hat sich bewährt und sie funktioniert«, so Georg Triepel, Leiter des Kunststoffspritzguss bei Hübner. Denn seit bereits knapp vier Jahren sammelt die Firma Erfahrungen mit der zentralen Versorgungsanlage des Ispringer Unternehmens.
Der Peripheriespezalist unterstützte Hübner bereits während der Bauphase bei der Konzeption und Umsetzung der Anlage, sodass die neue Halle auch auf die Förderanlage ausgelegt werden konnte. Die Anforderungen an diese definiert Triepel wie folgt: »Für uns waren neben einer bestmöglichen Granulattrocknung auch die Materialerkennung bzw. Codierung wichtig.« Da das Unternehmen fast ausschließlich Material verwendet, das getrocknet werden muss, war zudem ein entscheidender Faktor, dass jegliches Rohmaterial individuell vorbereitet wird. Bis das Rohmaterial an der Maschine angelangt ist, stellt die Granualttrocknung einen wichtigen Zwischenschritt dar. Um die Wege möglichst kurz zu halten, wurde die Trocknungsanlage in unmittelbarer Nähe zum Materiallager auf einer Bühne installiert.
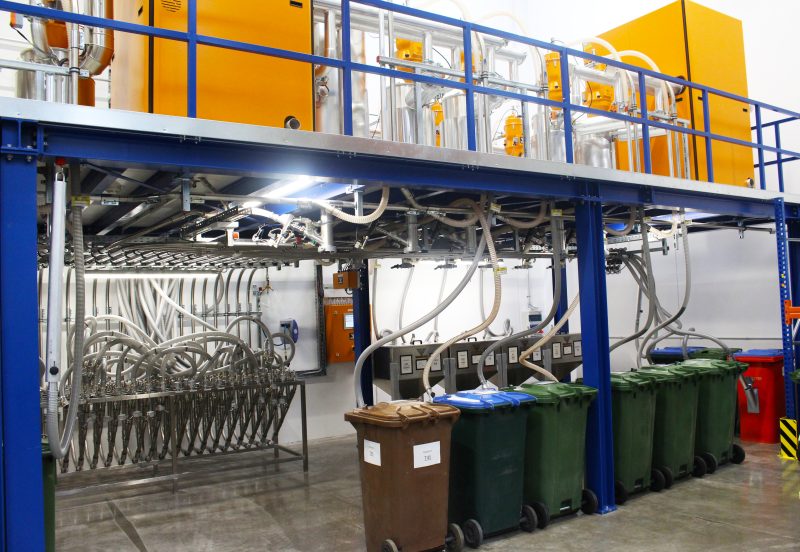
Der kompakte und doch ergonomische Aufbau der gesamten Materialtrocknungs- und -fördertechnik auf zwei Etagen (Bild: Koch-Technik).
Direkt angebundene Trocknungsanlage
Ein Bestandteil der Anlage sind zwei Trockenlufttrockner vom Typ »CKT« mit einer maximalen Trockenluftmenge von 300 und 500 Kubikmetern pro Stunde, an welche 15 Trocknungstrichter mit Volumen von 40 bis 400 Litern angebunden sind. Unter den jeweiligen Trocknungsbehältern befinden sich Oktabins oder Big Packs zur Entleerung des Granulats. Die Trockner sind frequenzgesteuert und regeln sich dadurch selbstständig um den Prozentanteil des entnommenen Materials aus den Behältern herunter. Somit wird in diversen Behältern die gleiche Trockenluftmenge gefördert. Um zu vermeiden, dass Granulat kaputtgeht, wird immer nur dann Material gefördert, wenn dieses die benötigte Restfeuchte erreicht hat. »Es wird immer nur das Material getrocknet, das auch tatsächlich benötigt wird. Wird Granulat dem Trocknungsprozess ab- bzw. zugeführt, errechnet der Trockner die benötigte Trockenluft neu«, erklärt Triepel. Dadurch erhält der ganze Trocknungsvorgang einen energiesparenden Nebeneffekt. Aufgrund der neuen Hallengröße hätte Hübner sogar noch Platz für weitere Behälter.
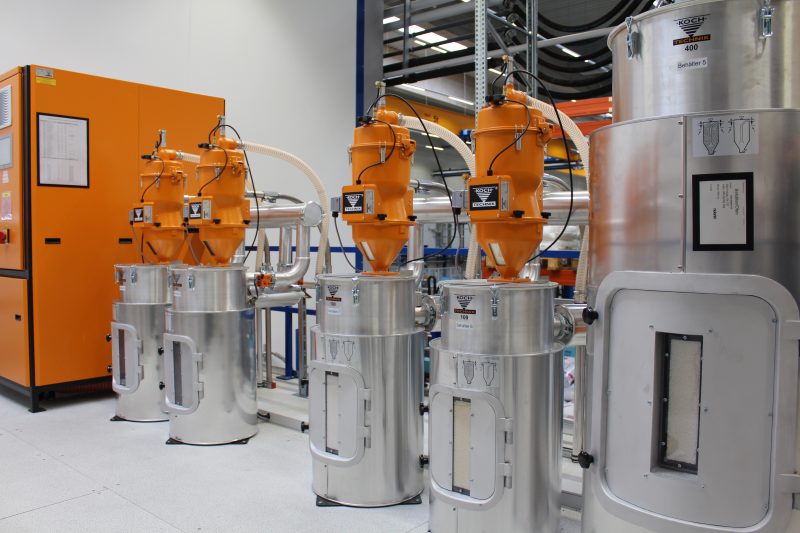
Die Trocknungstrichter besitzen ein Volumen von 40 bis 400¬l und sind an die Trockner angebunden. Unter den Fördergeräten befinden sich Zwischentrichter, die Handling- und Qualitätsvorteile bieten sollen (Bild: Koch-Technik).
Energiesparend und maschinenbezogen
Koch-Technik verbaut in die Systeme zudem die speziell entwickelte »Öko«-Anlagensteuerung, wodurch das Material vor Übertrocknung geschützt und gleichzeitig geschont wird. Das System verriegelt bei entsprechenden Temperaturen die Zu-/Abluft, und die Heizung schaltet automatisch ab. Die Behälter befinden sich dann solange im Absenkmodus bis Material entnommen wird. Peter Albrecht, bayerischer Vertreter von Koch-Technik, weist an dieser Stelle auf eine wichtige Neuerung hin: »Vorher lief der Trockner für sämtliche materialführenden Behälter immer auf voller Leistung. Jetzt wird nur die Leistung abgerufen, die auch tatsächlich gebraucht wird.« Seine Aussage konkretisiert er: »Obwohl etwa nur 10 Prozent des Rohmaterials gebraucht wurde, lief der Trockner auf 100 Prozent.« Außerdem besteht die Möglichkeit, an den Trocknern eine Materialdatenbank zu installieren – ein weiterer Aspekt der von großer Bedeutung für Triepel ist. Denn gerade für Unternehmen, die eine Vielzahl von Granulaten im Einsatz haben, ist es wichtig den Überblick zu behalten und so Einstellungsfehlern vorzubeugen.
Durch die Codierung des Materials sind dessen Eigenschaften und Verarbeitungsparameter automatisch hinterlegt, wodurch ein hohes Maß an Ordnung geschaffen wird. Wird ein Material ausgewählt, gibt der Trockner automatisch die Werte vor und kann es dem jeweiligen Trocknungsbehälter zuordnen. Eine Materialprüfung findet direkt am Material- oder Trocknungsbehälter statt. Um zu verhindern, dass nicht getrocknetes Material in der Leitung zurückbleibt, wird diese mithilfe der Leersaugung spezifischer Materialleitungen organisiert. »Gleiches gilt für Behälter, in denen nur ungetrocknetes Material gelagert wird«, ergänzt Albrecht. Der Umsteckbahnhof unterhalb der Bühne verteilt das Granulat über insgesamt drei Kilometer lange Edelstahlrohre zur Hallenmitte und von dort aus zur jeweiligen Spritzgießmaschine. Dies geschieht mit einer Geschwindigkeit von 20 bis 25 Metern pro Sekunde in einem Zeitraum von fünf bis sieben Sekunden. Um variabel hinsichtlich dieses Systems bleiben zu können, ist die Halle sternförmig angeordnet.
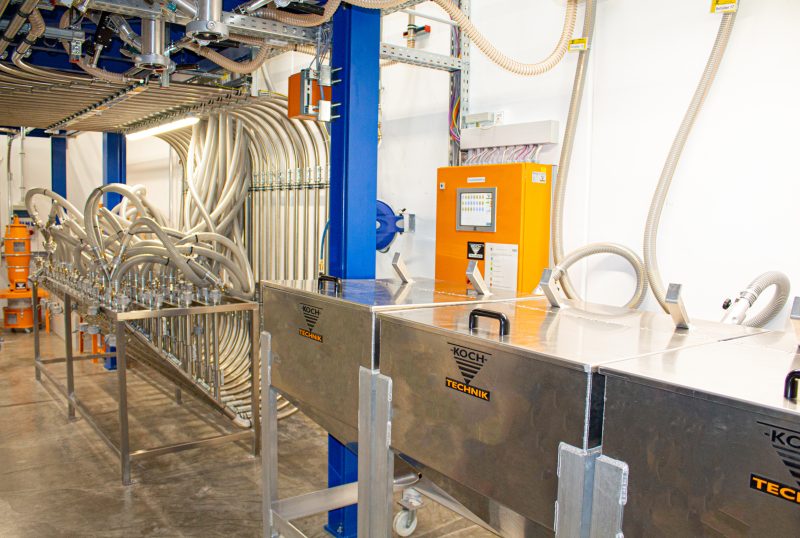
Herzstück der zentralen Materialversorgung ist der Umsteckbahnhof mit verwechslungssicherer Materialcodierung (Bild: Koch-Technik).
Taupunktgesteuerte Trocknung mit automatischer Umschaltung
Für das Trocknen des Granulats ist eine spezielle Trockenluft notwendig. Um diese zu erzeugen, arbeiten die Trockner taupunktgesteuert. Ein Trockenmittel entzieht der Luft, welche zuvor rückgeführt wurde, Feuchtigkeit. Parallel zu diesem Prozess findet die Regeneration einer zweiten Trockenmittelpatrone statt. Bei Hübner arbeiten die Trockner mit einem Taupunktbereich von -30 bis +60 Grad Celsius. Überschreitet die zu trocknende Luft den Schwellenwert -30 Grad Celsius im Trocknungskreislauf, erfolgt eine Umschaltung in den Regenerationskreislauf. Dieser selbstständige Umschaltprozess spart viel Energie ein.
Koch-Technik bietet ein Baukastensystem, das vor allem Flexibilität verspricht. So können beispielsweise Fördergeräte, Zwischentrichter oder Dosierstationen beliebig miteinander kombiniert werden. Ein wesentliches Charakteristikum ist der unter den eigentlichen Förderbehältern verbaute Zwischentrichter. »Bei anderen Lösungen wird der Förderabscheider direkt auf den Trocknungsbehälter gesetzt, der Auslassdurchmesser bzw. der Durchgang, durch den die Luft letztendlich fließt, ist dadurch sehr groß. Es steigt sämtliche trockene Luft nach oben, was wir so nicht wollen«, erläutert Albrecht. Zumeist liegt dann eine Verklumpung des Materials vor. Dadurch öffnet und schließt die Materialauslassklappe oft ungewollt. Koch-Technik wirkt dem durch seinen Zwischentrichter entgegen. Außerdem bleibt das Umklappen des Deckels samt des Abscheiders aus. Albrecht betont zusätzlich, dass das Ispringer Unternehmen prinzipiell auf Scharnierbehälter Wert legt.
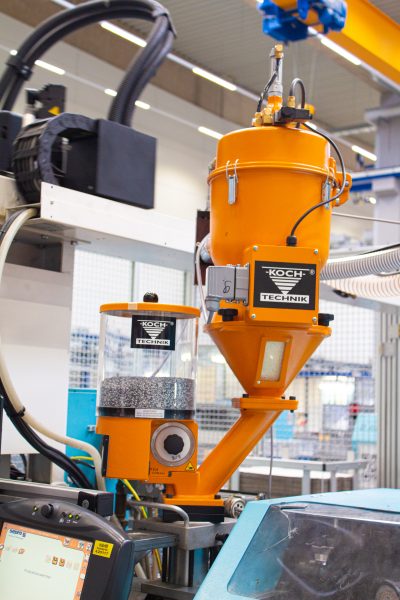
Förderabscheider und Masterbatch-Dosiereinheit auf der Spritzgussmaschine (Bild: Koch-Technik).
Materialförderung mit konstanter Geschwindigkeit
Um das Material fördern zu können, muss ein gewisser Unterdruck erreicht werden. Hierfür sind zwei Drehkolbenpumpen mit einer maximalen Leistung von 5,1 Kilowatt zuständig. Die Pumpen sind mit einem Entstauber ausgestattet, der Mikropartikel bis zu einer Größe von vier Mikrometern in einem Zentralfilter sammelt. Jeweils eine Pumpe sorgt für die Beförderung zum Trockner und die andere zur jeweiligen Spritzgießmaschine. Durch die verwendeten Drehkolbenpumpen ist es zudem möglich, dass das Material unabhängig vom Förderweg immer mit der gleichen Geschwindigkeit transportiert wird. »Die Pumpen sind luftgelagert, nicht ölgelagert, wie beispielsweise bei Seitenkanalverdichtern, bei denen das Material auch schubweise gefördert wird«, fügt Albrecht an. Das an der Spritzgießmaschine ankommende Granulat wird durch die im Materialeinzugsschacht gelegenen Förderabscheider von der Förderluft getrennt. Abhängig von der Maschinengröße können die Volumen der Abscheider divergieren. Darüber hinaus kann je nach Maschine das Rohmaterial über volumetrische Dosierstationen mit Farbgranulat eingefärbt werden. Um die einzelnen Komponenten während des Vorgangs überwachen zu können, wird ein externes Display verwendet, das die verschiedenen Betriebszustände aufzeigt. Durch farbige Darstellungen wird erkennbar, welche Trocknungsbehälter derzeit in Betrieb sind.
Georg Triepel ist mit der Zusammenarbeit nach wie vor sehr zufrieden und erinnert sich gerne an den Beginn des Bauprojekts zurück: »Wir konnten uns dabei voll und ganz auf das Knowhow von Koch-Technik verlassen. In unserem Geschäftsbereich ist Flexibilität besonders wichtig. Flexibilität, die bei der Umsetzung der gesamten Anlage gezeigt wurde.«