Symbiose von Software und Spritzgießmaschine
Spritzgießmaschinen
Für zwei technisch sehr herausfordernde Kunststoffformteile ist maximale Prozessstabilität Voraussetzung dafür, dass am Ende die gewünschten Anforderungen an Maßhaltigkeit und Funktionalität erfüllt werden. Die Firma Borgmann GmbH setzt dabei auf verschiedene digitale Produkte von Engel.
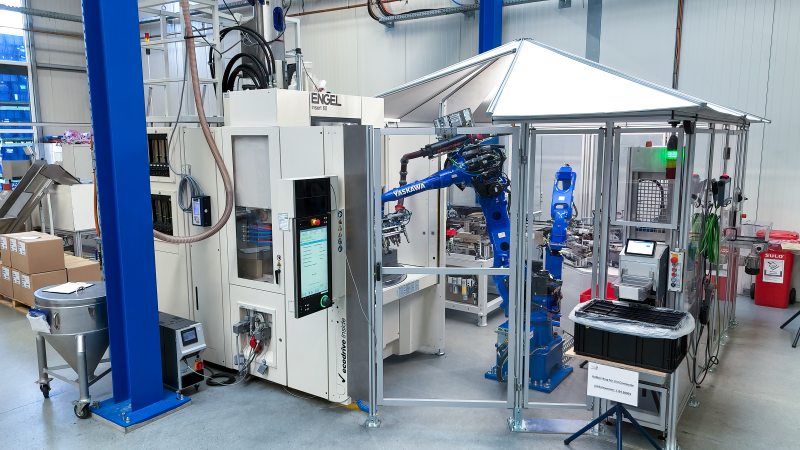
Diese vollautomatisierte Fertigungszelle produziert einen Stecker für die Automotive-Industrie. Dabei trägt die KI-basierte Prozessüberwachung zur Sicherung der hohen Qualität bei (Bild: Engel).
Die im Jahr 1992 gegründete Kunststofftechnik Borgmann GmbH aus dem niedersächsischen Bersenbrück produziert Kunststoffteile mit insgesamt 42 Spritzgießmaschinen mit Schließkräften von 28 bis 1000 Tonnen. In der modernen Kunststoffverarbeitung, zu der auch ein interner Werkzeugbau und eine eigene Konstruktionsabteilung gehören, halten mehr und mehr digitale Produkte Einzug.
Neue Lösungen sind gefordert
Stefan Borgmann, technischer Leiter des Betriebs, erläutert anhand von zwei verschiedenen Produktionszellen die Vorteile des Einsatzes der digitalen Assistenzsysteme in zwei gänzlich unterschiedlichen Fertigungsprozessen: »Die Geometrien werden immer komplexer, die geforderten Toleranzen immer kleiner und die zu verarbeitenden Materialien werden für den Verarbeiter immer anspruchsvoller.«
Neue Herausforderungen verlangen nach neuen Lösungen, die er durch Maschinenversuche im Engel-Technikum in Schwertberg erhalten hat. Ein wichtiger Aspekt, der für den vielfältigen Einsatz digitaler Assistenzsysteme wie »iQ process observer« spreche, sei die Transparenz, die man dadurch im Produktionsprozess erhalte, versichert Borgmann. Diese Transparenz verschaffe dem Bedienpersonal sehr schnelle Reaktionszeiten, wenn es einmal im Prozess zu Unregelmäßigkeiten kommen sollte. »In erster Linie wollen wir in unseren Produktionsprozessen eine maximale Effizienz und Qualität erreichen«, betont er.
Die Firma Borgmann erhält durch den Einsatz von »iQ process observer« eine aufbereitete und übersichtliche Darstellung der aktuell relevanten Daten direkt an der Maschine. So bekommen die Prozesstechniker jede Sollwertänderung und Prozessabweichung in Echtzeit mit. Diese bilden dann die Basis, um Prozesse weiter zu optimieren und Abweichungen frühzeitig zu erkennen
Diffizile Spritzgießteile
Beim ersten beispielhaften Produkt handelt es sich um ein Mikroformteil: eine filigrane Verstellscheibe, die in der Möbelindustrie eingesetzt wird. Das Teil wiegt nur 0,02 Gramm und steuert die Zuführung eines Synthetiköls, mit dem der Grad der Dämpfung eines Scharniers feinjustriert wird. Gefertigt wird das Bauteil auf einer »e-victory 50/28«, eine Hybridspritzgießmaschine mit elektrischer Spritzeinheit und hydraulischer Schließeinheit, auf der Polyoxymethylen (POM) verarbeitet wird. Das dazugehörige Werkzeug verfügt über 16 Kavitäten und vier offene Heißkanaldüsen sowie einen Kaltkanal. Angespritzt wird es über einen Tunnelanguss.
Beim zweiten Formteil handelt es sich um ein Steckersystem für die Automobilindustrie. Das Material PA 66 GF 35 wird auf einer vertikal angeordneten Spritzgießmaschine des Typs »insert V 200/60 rotary« gefertigt. Diese ist mit einem Drehteller ausgestattet, auf dem die zwei unteren Werkzeughälften positioniert sind. Während die eine Werkzeughälfte für den Einspritzvorgang positioniert ist, wird parallel die andere Werkzeughälfte vollautomatisiert mit drei Kupferkontakten und Buchsen bestückt, bevor dann wieder der Einspritzvorgang umgesetzt wird. In nachgeschalteter Vollautomation wird noch eine Dichtlippe aus Silikon aufgebracht. Zudem erfolgt für jeden einzelnen Stecker eine Hochspannungs- und Dichtigkeitsprüfung. Unerlässlich ist für das Qualitätsmanagement die Taumelkreisprüfung, mit der die korrekte Anordnung der Stecker permanent überwacht wird.
Echtzeitanalyse vieler Parameter
»In Summe sind viele Parameter und deren Stabilität für die Qualität des Produktes verantwortlich«, so Stefan Borgmann. Für die permanente Kontrolle der Prozessstabilität sorgt »iQ process observer«. »Der Maschinenbediener muss sich an den Maschinen nicht jeden einzelnen Parameter aufrufen, um zu erfahren, wie der Status quo des Prozesses ist«, freut sich Borgmann über den Komfort.
Das System ist seit Sommer 2022 im Einsatz. »Alles, was numerisch erfasst werden kann, beispielsweise Forminnendrucksignale oder Energiemesswerte, wird vom System berücksichtigt«, erklärt Andreas Heckmann, der für Engel den Kunden in diesem Verkaufsgebiet betreut. Abweichungen in den unterschiedlichen Phasen des Spritzgießprozesses werden über ein Ampelsystem kenntlich gemacht und stellen dem Bedienpersonal mithilfe des konstanten Abgleichs der Prozesswerte übersichtlich mögliche Abweichungen dar. Diese KI-Lösung bietet dem Bedienpersonal in der Steuerung »CC300« auch Prozesshinweise zur Behebung des aufgetretenen Fehlers und zur Optimierung des Prozesses an.
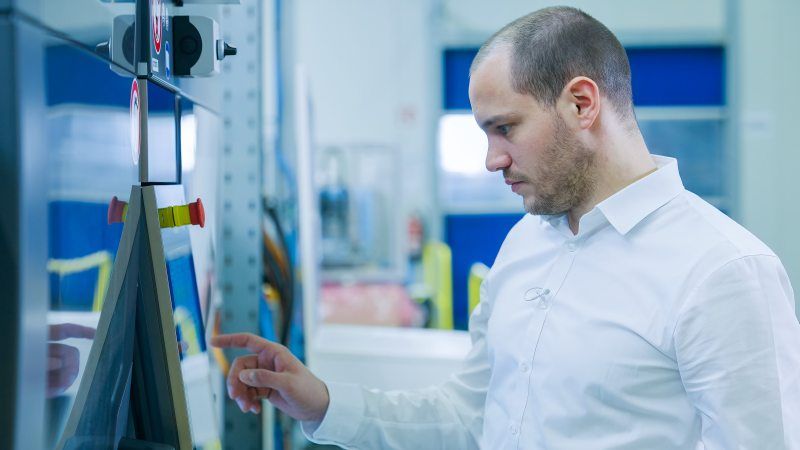
Schnell und übersichtlich: Stefan Borgmann sieht die aktuellen Prozessdaten auf dem Display der Steuerung »CC300« ein, die mithilfe von »iQ process observer« dargestellt werden (Bild: Engel).
Die Implementierung von »iQ process observer« war sehr komfortabel, wie sich Stefan Borgmann erinnert: »Wir haben die Maschine einfach in unser Netzwerk eingebunden und konnten dann bereits loslegen.« Ist die Maschine auch mit Engel verbunden, kann man tagesaktuell von den Neuerungen des Systems profitieren. Andreas Heckmann erwähnt an dieser Stelle die hohe Sicherheit dieser digitalen Verbindung, die den Prinzipien des Security-by-Designs folge und sehr hohen Standards entspreche: »Darüber läuft ebenfalls die Fernwartung der einzelnen Maschinen.«
Übersicht und Schnelligkeit
Als größte Vorteile nennt Bergmann die gute Prozessübersicht und die Schnelligkeit. »Wenn ich zur Maschine komme, genügt ein Fingertouch bei der Steuerung und ich sehe innerhalb einer Sekunde, was in dem Prozess Sache ist«, ist für ihn diese zentrale Prozessanalyse nicht mehr wegzudenken. Es wird einmal ein Referenzzyklus angelegt, der im System abgespeichert wird und dem System als Orientierung für die folgenden Spritzgießzyklen dient. »Darüber hinaus kann ich sehr schnell Sollwertänderungen ablesen und erkenne, wie sich diese im Spritzgießprozess auswirken – zum Beispiel wenn die Werkzeugtemperatur sinkt oder mehr Einspritzdruck benötigt wird.« Er betont an dieser Stelle, dass man die Informationen erhalte, bevor Schlechtteile produziert würden. »Kenntlich gemacht wird das über eine gelbe Ampel.«
Bei einem Klick auf das gelbe Ampelsymbol werden dann nur die Werte angezeigt, die das eigentliche Problem betreffen. »Das System wird natürlich immer schlauer, wofür das Know-how der lokal gespeicherten Daten genutzt wird«, liefert Heckmann die Begründung dafür, warum die Daten für die Weiterentwicklung des gesamten Systems elementar sind. Interessant sei das zudem für eine mehrschichtige Produktion mit unterschiedlichen Maschinenbedienern, denn es könne schnell nachvollzogen werden, ob manuell in den Prozess eingegriffen wurde und dadurch die Stabilität verloren gegangen sei. »Für uns ist es daher notwendig, intern Schulungen für die Nutzung des Systems durchzuführen, denn die Mitarbeiter sollen verstehen, dass ›iQ process observer‹ ihnen in erster Linie eine schnelle und übersichtliche Hilfestellung bietet«, erwähnt Borgmann. In Zeiten des Fachkräftemangels sei das ein Vorteil, weil der interne Aufwand dadurch pro Tag und Maschine um 30 Minuten in Bezug auf Fehleranalysen und Qualitätsprüfungen reduziert werde, wodurch Ressourcen für andere Tätigkeiten frei würden.
Ganzheitliche Lösung
Um die Prozesse nachhaltig abzusichern, verlässt sich Kunststofftechnik Borgmann auf sein geschultes Personal und setzt ergänzend immer mehr digitale Technologie des österreichischen Maschinenherstellers ein. »Für uns ist das eine sehr komfortable Lösung, um drohende Maschinenstillstände oder Produktionsunterbrechungen frühzeitig zu erkennen und zu vermeiden«, ist Stefan Borgmann von dieser ganzheitlichen Lösung nach wie vor überzeugt. In Kombination mit weiteren digitalen Lösungen des Maschinenherstellers haben sich neuartige Arbeitsweisen entwickelt, mit denen sich nachhaltig Produkte mit hoher Wiederholgenauigkeit fertigen lassen. »Wir produzieren in der Folge natürlich ressourcenschonender«, versichert er. »Es werden weniger Schlechtteile produziert, weil die Assistenzsysteme zuverlässig ihren Dienst verrichten.«
Durch den vielfältigen Einsatz der digitalen Lösungen konnte neben der Steigerung der Transparenz auch der Energieverbrauch um bis zu 50 Prozent reduziert werden. »Was an digitalen Produkten von Engel eingesetzt werden kann, finden Sie in unserer Produktion. Deren Einsatz ist kein Muss, hebt jedoch die Sicherheit des Prozesses und die Wiederholgenauigkeit der Qualität der gefertigten Formteile auf ein neues Level«, ist sich Borgmann sicher, den eingeschlagenen digitalen Weg in Zukunft fortzusetzen.