Kunststoff im Kreislauf halten
Recycling / Abfallbehandlung, Aufbereitung und Entsorgung
Die Qualitätsansprüche der Hansgrohe SE an die gefertigten Handbrausen und Duschgarnituren sind sehr hoch. Dies gilt vor allem für die galvanisierten Oberflächen, wo selbst der kleinste Kratzer schon zu Ausschuss führt. Bisher wurden die Bauteile von qualifizierten externen Partnern verwertet. Gemeinsam mit Impulstec hat das Unternehmen daher ein Verfahren entwickelt, bei dem 98 Prozent des Kunststoffs sowie das eingesetzte Metall wiederverwertet werden können.
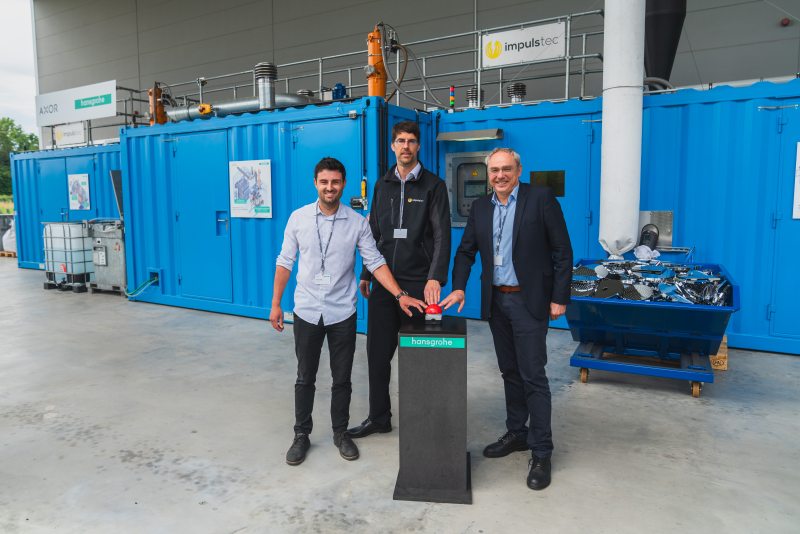
V. l.: Projektleiter David Zapf, Hansgrohe, Impulstec-Geschäftsführer Stefan Eisert und Frank Semling, Vorstand Operations Hansgrohe, nehmen die individuell entwickelte Recyclinganlage für galvanisierte Kunststoffe offiziell in Betrieb (Bild: Hansgrohe).
Offenburg liegt zwar nicht in Schwaben, trotzdem begrüßt am 14. Juni ein »schwäbischer Sommer« die Besucherinnen und Besucher des Hansgrohe-Werks in Offenburg-Elgersweier mit Temperaturen unter 20 Grad Celsius und leichtem Nieselregen. Man hat sich hier eingefunden, um der offiziellen Inbetriebnahme einer Weltneuheit beizuwohnen: der ersten Recyclinganlage für galvanisierte Kunststoffe.
Nachhaltigkeit als Unternehmensziel
Sein größtes Werk, in dem das Sanitärunternehmen Hand- und Kopfbrausen im Spritzgießverfahren herstellt, wurde 1990 im Industriegebiet Offenburg-Elgersweier eröffnet. Bereits vor über 30 Jahren war die Planung des Werks vom Nachhaltigkeitsgedanken geprägt. »Eins der Gebäude wurde mit der damals größten dachinstallierten Fotovoltaikanlage Deutschlands errichtet«, erläutert Jörg Reiff, stellvertretender Leiter der »Hansgrohe Aquademie« während des Betriebsrundgangs. »Der Energiebedarf in unseren deutschen Werken beträgt circa 45 Gigawatt jährlich. Davon können wir hier in Offenburg rund 473 Megawattstunden mit der Fotovoltaikanlage und circa 10 Gigawatt aus einer Windkraftanlage decken, die im neu gebauten Badenova-Windpark Kallenwald im Schwarzwald steht. Diesen erneuerbaren Strom bezieht Hansgrohe als regionaler Abnehmer exklusiv über einen Dienstleister. Insgesamt arbeiten bereits heute alle unsere Werke klimaneutral, und circa 50 Prozent des eingesetzten Granulats basieren nicht mehr auf Erdöl.«
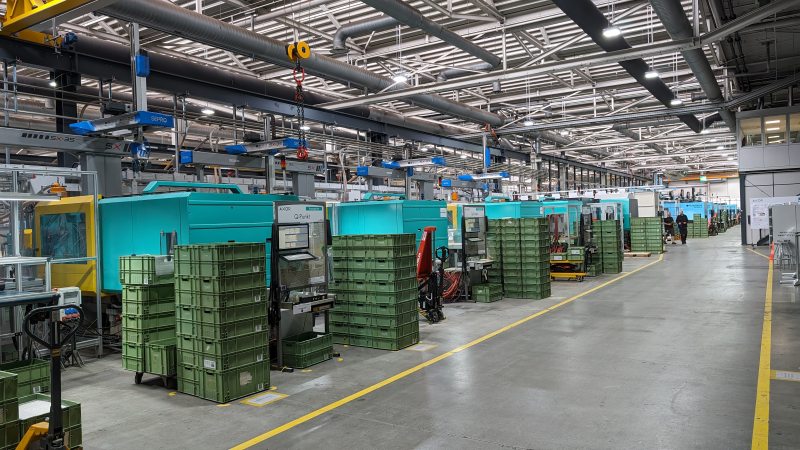
62 Spritzgießmaschinen fertigen im Hansgrohe-Werk die Produkte (Bild: Kuhn Fachverlag).
»Das Werk wurde von Anfang an nachhaltig geplant. So wurde zum Beispiel eine Wasseraufbereitungsanlage für das Grauwasser implementiert. Im Jahr 1991 wurde ein Solarturm zu Forschungszwecken auf dem Gelände errichtet. Er ist aus Holz gebaut und die Fenster haben einen für damalige Verhältnisse sensationellen K-Wert von 0,5«, ergänzt Frank Semling, Vorstand Operations.
Von der Spritzgießmaschine zur Galvanisierung
Kunststoff ist leicht sowie formbar und damit ein ideales Material für die Brausen. Alle Produkte werden aus ABS gefertigt, die Materialversorgung der insgesamt 62 Spritzgießmaschinen erfolgt über eine zentrale Rohrleitung. Daneben werden im Werk auch Armaturen aus glasfaserverstärktem Kunststoff hergestellt, der mittlerweile das klassische Messing abgelöst hat.
Die Werkzeuge für die im Spritzgießverfahren produzierten Brausen werden im eigenen Werkzeugbau gefertigt. »Nur so können wir sicherstellen, dass die Rohlinge mit einer perfekten Oberfläche für die anschließende Galvanisierung die Spritzgießmaschine verlassen«, erläutert Reiff. Die Brauserohlinge werden direkt nach dem Spritzgießen auf speziell für die jeweiligen Modellreihen angepassten Galvanogestellen fixiert. So gelangt alle sieben Minuten ein Trägergestell in die Galvanik.
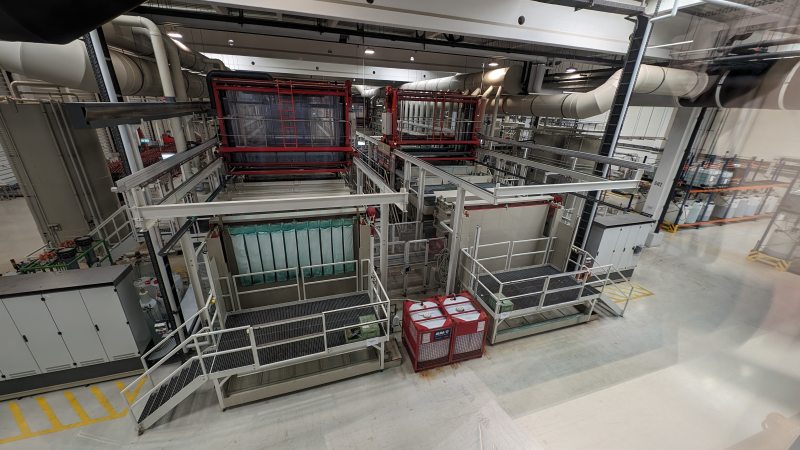
Die Galvanikanlage kann bis zu 570.000 Quadratmeter Oberfläche im Jahr galvanisieren (Bild: Kuhn Fachverlag).
Vor der metallisierten Oberfläche werden die Kunststoffteile mittels Beizebad aufgeraut. Durch das anschließende Bad im Aktivator werden Palladium und Zinn absorbiert, im Anschluss wird Zinn wieder abgelöst, wodurch eine elektrisch leitende Oberfläche entsteht. Nach diesen Vorbereitungen erhalten die Teile der Reihe nach in Kupfer-, Nickel- und Chrombädern ihre endgültige glänzende und kratzbeständige Oberfläche. Der gesamte Prozess dauert circa zweieinhalb Stunden.
»Unsere Galvanikanlage umfasst in etwa die Größe von zwei Fußballfeldern. Die Anlage fährt im Dreischichtbetrieb und arbeitet mit Doppelwarenträgern, sodass wir bis zu 570.000 Quadratmeter Oberfläche im Jahr galvanisieren können. Bei der Planung wurden auch Flächen für eine spätere Erweiterung der Anlage berücksichtigt«, erläutert Thorsten Pohl, Vice President Technical Engineering and Technology bei Hansgrohe.
Ziel: Kunststoffe wiederverwerten
Nach der Galvanisierung folgt die manuelle optische Kontrolle, die aufgrund der spiegelnden Oberfläche auch heute noch nicht mithilfe von Bildverarbeitungssystemen durchgeführt werden kann. Trotz eines ausgereiften Galvanisierungsprozesses gibt es immer wieder Ausschuss. Selbst die kleinste Oberflächenbeschädigung sorgt für die Ausschleusung des Teils. Besteht eine Brause die optische Beurteilung, wird mithilfe von Wechselbändern geprüft, ob das Metall auch vollflächig am Kunststoff haftet.
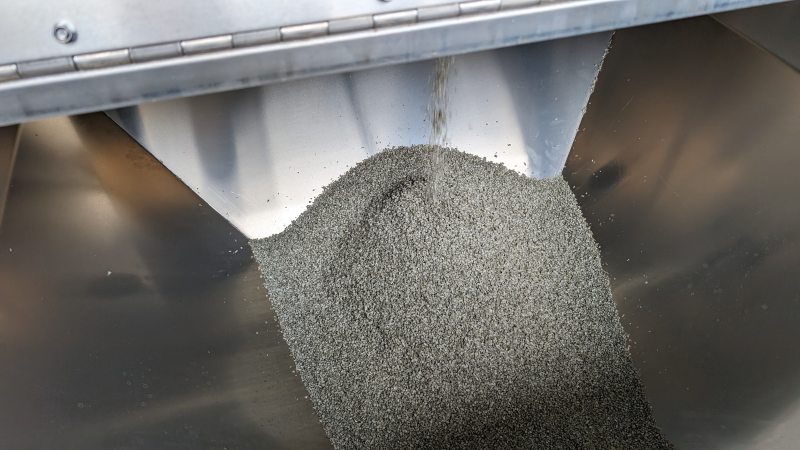
Die Recyclinganlage trennt sauber den Kunststoff, aus dem im Werk wieder neue Produkte entstehen (Bild: Kuhn Fachverlag).
Bis zum Projektbeginn 2019 stand das thermische Recycling im Vordergrund, um die wertvolle Metallbeschichtung zurückzugewinnen. Das Unternehmen wollte jedoch den Wertstoffkreislauf am Standort schließen und suchte daher nach einem geeigneten Verfahren zum Recycling der Ausschussteile.
Kompakte Recyclinganlage mit Vorbildcharakter
Im Rahmen seiner Masterarbeit analysierte David Zapf, Specialist Surface Technology, mehrere potenzielle Verfahren, um die feste Verbindung von Metall und Kunststoff wieder zu trennen.
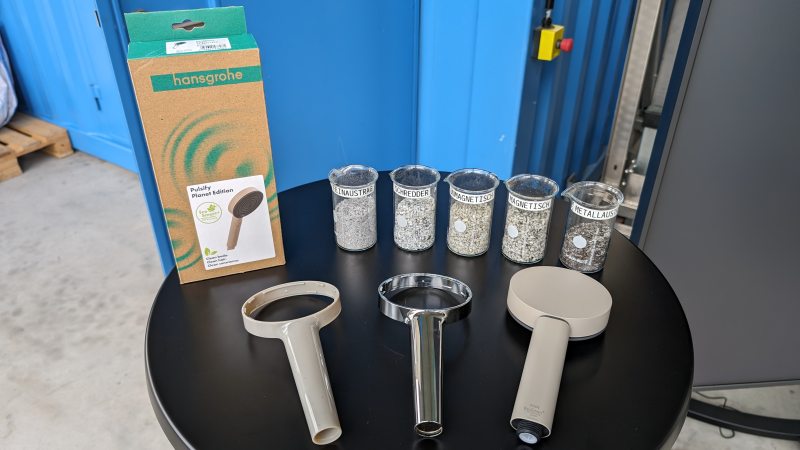
Das geschredderte Material durchläuft mehrere Stufen. Aus dem Rezyklat werden wieder galvanisierte Duschköpfe (links und Mitte) oder Produkte aus der Reihe »Planet Edition« hergestellt (rechts und links oben; Bild: Kuhn Fachverlag).
Als technisch geeignetes und vor allem wirtschaftlichstes Verfahren kristallisierte sich bei diesem Prozess das Schockwellenverfahren heraus. Durch die in Kooperation mit dem Anlagenbauer lmpulstec GmbH entwickelte Recyclinganlage lassen sich die verchromten Ausschussteile so aufbereiten, dass der entschichtete ABS-Kunststoff zu 98 Prozent direkt vor Ort in der Kunststoffspritzerei wieder zur Herstellung von Neuteilen zur Verfügung steht.
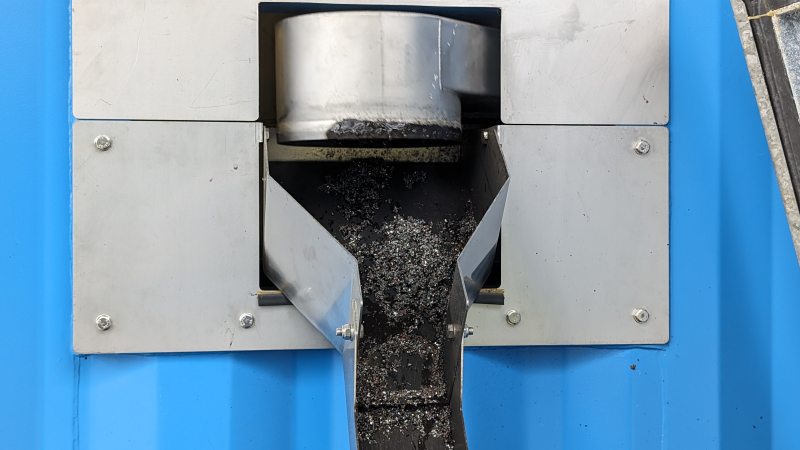
Die hochkonzentrierte Metallfraktion geht zur Verhüttung in den Verkauf (Bild: Kuhn Fachverlag).
Bei der innovativen Anlage wird die Technologie zur elektrohydraulischen Zerkleinerung angewendet. Dabei werden die verchromten Ausschussteile durch Schockwellenbehandlung in Verbindung mit einer Vorzerkleinerung und magnetischer Separation entschichtet. »Als Ergebnis entsteht zum einen eine hochkonzentrierte Metallfraktion, die im wesentlichen Kupfer und Nickel enthält. Diese geht zur Verhüttung in den Verkauf. Die wertvollen Metalle werden so wieder zu 100 Prozent dem Rohstoffkreislauf zugeführt. Zum anderen erhalten wir den entschichteten ABS-Kunststoff, den wir zur Herstellung von Neuteilen verwenden. Hier nutzen wir das Material direkt vor Ort in unserer Kunststoffspritzerei und können so den Wertstoffkreislauf am Standort schließen«, erläutert Projektleiter Zapf.
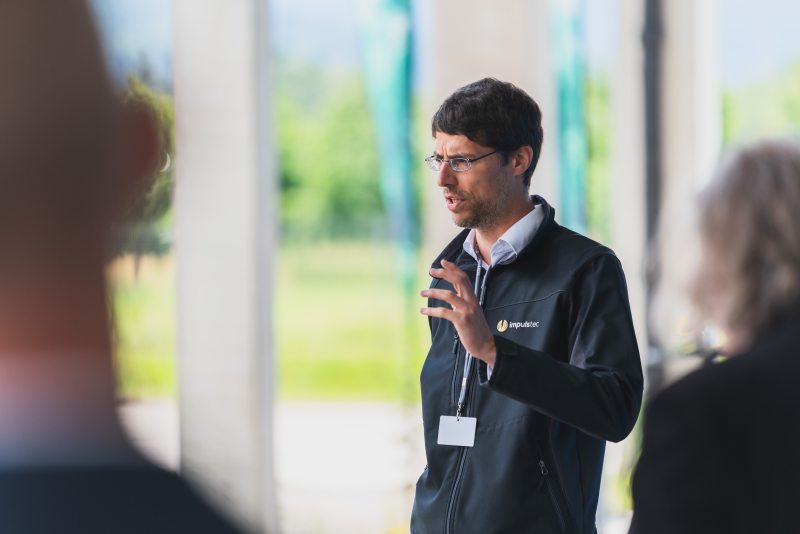
Impulstec-Geschäftsführer Stefan Eisert erläuterte die technischen Details der Anlage (Bild: Hansgrohe).
»Als Experte für Hightech-Recycling sind wir auf komplexe Aufgaben bei der Entwicklung von Entschichtungstechnologien spezialisiert, zum Beispiel für das Batterie- oder Solarmodul-Recycling. Die Einrichtung bei Hansgrohe ist eine echte Weltneuheit, so eine Anlage gab es bisher nirgends«, betont Impulstec-Geschäftsführer Stefan Eisert bei der feierlichen Vorstellung in Offenburg.
Die Recyclinganlage wurde für eine jährliche Kapazität von 100 Tonnen verchromtem Kunststoff ausgelegt. Aus dem daraus gewonnenen Rezyklat können rein rechnerisch eine Million neue Handbrausen gefertigt werden.