Materialversorgung: Anlagenwechsel im laufenden Betrieb
Dosier-, Misch- und Förderanlagen
Die Produktpalette des Braun-Werks Walldürn der Procter & Gamble Manufacturing GmbH wird ständig erweitert. Mit ihr wächst auch die Zahl der Design- und Funktionsteile, die auf über 70 Spritzgießautomaten gefertigt werden. Als die Versorgung der Maschinen mit den vielen verschiedenen Materialien zu unflexibel wurde, wurde in eine neue Anlage von Koch-Technik investiert. Der Wechsel erfolgte ohne Stillstand der rund um die Uhr laufenden Produktion.
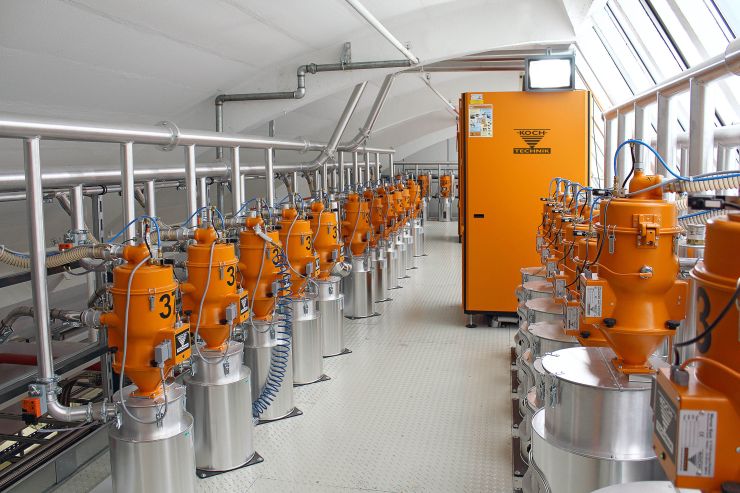
Granulattrocknung: Die zentrale Anlage mit insgesamt drei Trockenlufttrocknern, die 38 Trocknungsbehälter mit einer Trockenluftmenge von insgesamt bis zu 1600 m³/h versorgen. Bild: Koch-Technik
»In unserer Kunststoffteilefertigung produzieren wir mit hoher Fertigungstiefe alles, was bei P&G mit elektrischer Rasur und Epilation zu tun hat«, erklärt Frank Breunig, als Projektingenieur bei P&G Braun für das Projekt zur Umstellung der Materialversorgung verantwortlich. In einer 24/7-Produktion wird auf über 70 Spritzgießautomaten mit Schließkräften zwischen 50 bis 300 Tonnen produziert. Die gespritzten Teile sind mit 0,5 bis 50 Gramm eher leicht, aber die Vielzahl der verwendeten Materialien wie ASA, ABS, PC, PC-PET, PA, PBT, POM, PPS und PP, zum Teil auch faserverstärkt, ist beachtlich. Jeden Tag werden für die Spritzgießfertigung über drei Tonnen Granulat in Oktabins und als Sackware bereitgestellt. Die vielen Materialien erfordern eine flexible Materialversorgung mit konstant gleichbleibender Qualität des getrockneten Materials. Und bei beiden Punkten, insbesondere bei der Flexibilität, stieß man schnell an die Grenzen der bisherigen Anlage, weshalb nach einer neuen, zeitgerechten Lösung gesucht wurde.
Ein zusammengestelltes Projektteam definierte klare Vorgaben für eine neue Materialversorgung: »Jedes Material auf jeder Maschine, innerhalb kürzester Zeit, reproduzierbar und unterhalb der maximal zulässigen Restfeuchte«, umreißt Frank Breunig knapp den für ihn wichtigsten Aspekt. Neben der zentralen Förderung sollte auch die Materialverteilung automatisiert ablaufen und Sicherungsmechanismen sollten schon bei der Materialaufgabe falsches Material verhindern. Ganz wichtig war, auch im Hinblick auf die digitale Transformation, die Möglichkeit der zentralen Überwachung, verbunden mit der Option zur Einbindung in das interne ERP-System. Der Umbau sollte zudem zeitgleich mit der auf Volllast laufenden Produktion über die Bühne gehen.
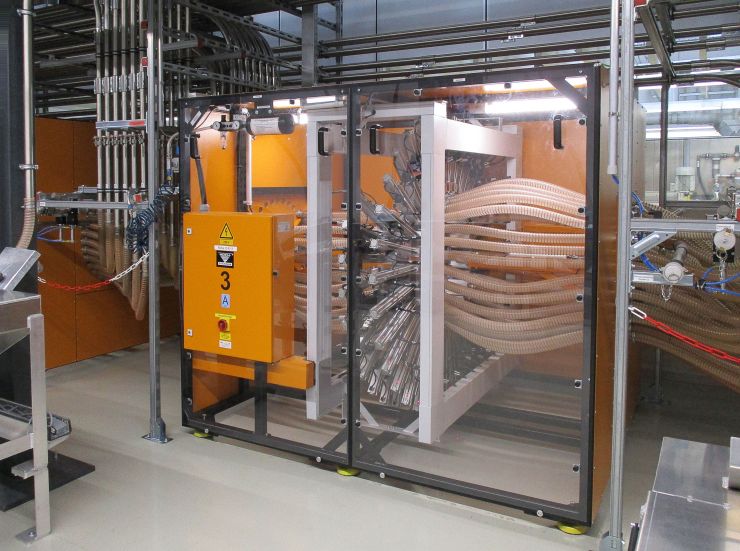
Materialverteilung: Über die »Navigatoren« kann jede Bedarfsstelle in der Spritzerei mit jedem vorbereiteten Material versorgt werden. Bild: Koch-Technik
Komplett neues Versorgungskonzept mit Industrie 4.0
Koch-Technik plante eine neue Materialversorgung auf Basis von Saugförderung durch ein zentral erzeugtes Permanentvakuum. Ein solches System hat eine Vakuum- beziehungsweise Saugleitung und mehrere Förderleitungen für den Materialtransport. Das Material, hier ausgelegt auf Granulate mit einer Korngröße zwischen zwei und vier Millimetern und einem Schüttgewicht von 0,6 bis 0,8 kg/dm³, kann so über große Entfernungen gefördert werden. Um jede Maschine mit jedem Material versorgen zu können, ist die gesamte Anlage aus fünf Einzelsystemen zusammengesetzt: Das erste System versorgt die Trocknungsbehälter der neuen Granulattrocknung von Koch-Technik, und über die vier anderen Systeme ist es möglich, jedes vorgetrocknete Material zu jeder Bedarfsstelle in der Spritzerei zu transportieren. Die Planung nach Bedarfsstellen ist nötig, weil viele Funktionsteile in Mehrkomponentenspritzguss gefertigt werden und eine Spritzgießmaschine dementsprechend über mehrere Bedarfsstellen verfügt. Folglich wird jeder Bedarfsstelle ein Förderabscheider zugeteilt, der direkt auf der Spritzgießmaschine das Material ansaugt und von der Förderluft trennt. Um eine erneute Befeuchtung von hygroskopischem Material im Leitungssystem zu verhindern, ist im materialführenden System eine doppelte Leersaugung geplant.
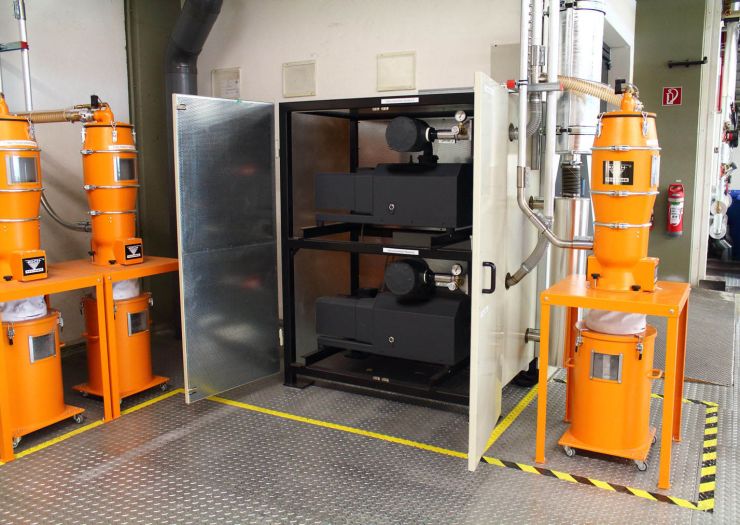
Die Vakuumpumpen arbeiten frequenzgeregelt,
was den Energieverbrauch senkt und die materialführenden Leitungen vor Verschleiß
schützt. Bild: Koch-Technik
Vier automatisierte Materialleitsysteme vom Typ »Navigator« verteilen das Material, ausgehend von der Granulattrocknung, auf die Spritzgießmaschinen. Alle Steuerungen der Anlagen werden letztendlich in der Koch-Visualisierung zusammengeführt, eine Software zur Überwachung der Materialversorgung und Einbindung in das interne ERP-System.
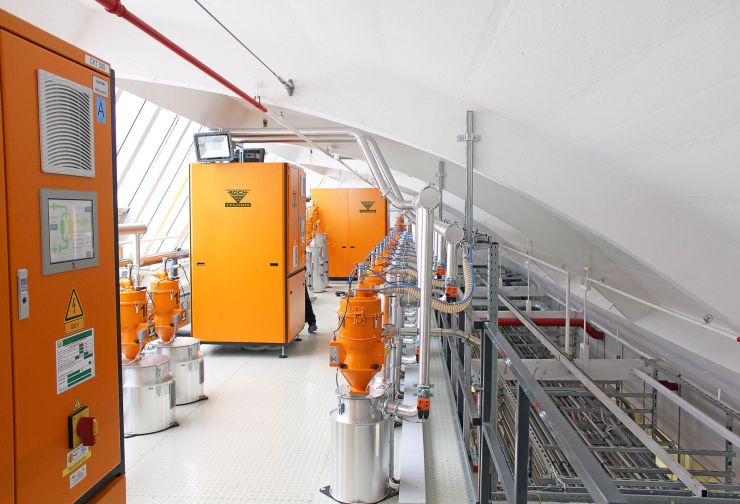
Alle Behälter der Trocknungsanlage wurden in den Boden der Bühne eingelassen. Bild: Koch-Technik
Die zentrale Anlage zur Granulattrocknung ist auf einer in die Halle eingespeisten, großzügigen Bühne installiert. Drei große Trockenlufttrockner vom Typ »CKT« mit »Öko«-Anlagensteuerung versorgen hier 38 Trocknungsbehälter mit einer Trockenluftmenge von insgesamt bis zu 1600 m³/h. Erzeugt wird die Trockenluft taupunktgesteuert, das heißt in einem Kreislauf durchströmt trockene Luft das Granulat in den Trocknungsbehältern. Dabei nimmt die Luft die Feuchtigkeit des Granulats auf und gibt sie später an ein Trockenmittel ab. Gleichzeitig wird in einem zweiten Kreislauf ein gesättigtes Trockenmittel regeneriert. Sobald die zu trocknende Luft den Taupunkt von -30 Grad Celsius erreicht, was einem Wassergehalt der Trockenluft von 0,33 Gramm pro Kubikmeter entspricht, schaltet die Steuerung zwischen den Kreisläufen von Trocknung und Regenerierung um. Die Vorteile sind geringerer Energieverbrauch und gleichbleibende Trocknungsqualität. Damit das Granulat materialschonend getrocknet und nicht übertrocknet wird, ist die Koch-eigene »Öko«-Anlagensteuerung integriert. Sie erkennt, ob das Material die zur Verarbeitung notwendige Restfeuchte erreicht hat, und nimmt dann den Behälter aus dem Trocknungskreislauf oder schaltet ihn bei Bedarf wieder zu. Neben dem Schutz vor Übertrocknung bedeutet das auch eine hohe Energieeinsparung. Auch die frequenzgeregelten Gebläse tragen zur energiesparenden Trocknung bei, denn sobald ein Behälter in den Ruhezustand versetzt wird, reduzieren sie automatisch den Trockenluftstrom.
Automatische Materialverteilung
Eine der wichtigsten Anforderungen war Flexibilität bei der Materialverteilung, also die Weichenstellung für getrocknetes Material direkt zur Spritzgießmaschine. Bisher waren hohe Verluste bei Materialwechseln an der Tagesordnung. Nach Marktvergleichen entschied man sich für den »Navigator« von Koch-Technik. Diese Materialverteilung ist hochflexibel, sicher, frei von Verunreinigungen, spart die Zeit des Umkuppelns und ist damit besonders für eine Produktion geeignet, in der viele verschiedene Materialien verarbeitet werden und mehrere Materialwechsel pro Maschine an der Tagesordnung sind. Bis zu 40 eingehende Material- und weiterführende Maschinenleitungen kann ein »Navigator« verwalten. Werden zusätzliche Ein- oder Ausgänge benötigt, können mehrere »Navigatoren« eingesetzt werden, wie hier bei P&G Braun, wo jedes Einzelsystem mit einem Materialleitsystem ausgestattet ist, also insgesamt vier »Navigatoren« mit durchschnittlich je 32 Materialeingängen, sodass insgesamt jede Bedarfsstelle in der Spritzerei mit jedem vorbereiteten Material versorgt werden kann. Zur Weichenstellung fahren die pneumatischen Schieber des »Navigators« einfach die gewünschte Material- und die Maschinenleitung in der Mitte zusammen. Die Leitungen werden für die Dauer des Materialtransports direkt miteinander verbunden. Jeder Fördervorgang wird registriert und in der Visualisierung dokumentiert.
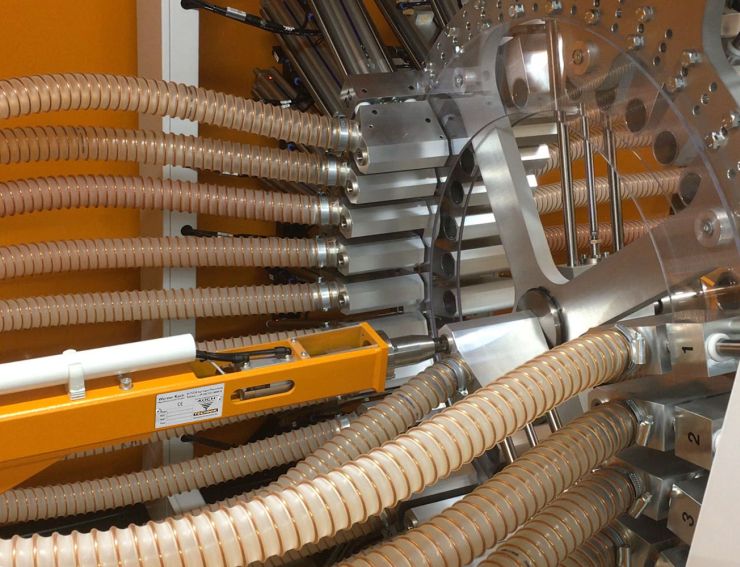
Zur Materialverteilung fahren die pneumatischen Schieber des Navigators die
gewünschte Material- und die Maschinenleitung in der Mitte zusammen. Bild: Koch-Technik
Mit der Visualisierung lassen sich alle Aktivitäten der eingebundenen Peripherie in Echtzeit nachverfolgen. Dank modularen Aufbaus ist sie auf die Materialversorgung von P&G Braun zugeschnitten und überwacht die gesamte Anlage. Ein zentraler Rechner dient als Leitstand, auf dem Monitor können alle Stationen des Materials visuell verfolgt und bei Bedarf angepasst werden. Alle Aktivitäten der Anlage werden aufgezeichnet und zertifizierungssicher gespeichert. So lässt sich jede Materialcharge bis zur Materialaufgabe zurückverfolgen. Zudem bietet die Visualisierung eine Schnittstelle zum ERP-System und ebnet damit den Weg zu einer digitalen Gesamtlösung in Richtung Industrie 4.0.
Die Visualisierung setzt beim Punkt Materialsicherheit bei der Materialaufgabe an. Direkt verbunden mit der Trocknerbefüllung und den Optionen zur Materialsicherheit, speichert die Software alle Materialwechsel und verifiziert die Materialzuordnungen an den Behälter- und Stellplatzsicherungen. Über Barcode-Scans und einen Datenabgleich wird ein Einfüllen von falschem Material schon bei der Materialaufgabe, also dem Eingang zur gesamten Materialversorgungsanlage, unterbunden. Ein Container öffnet sich erst, wenn die Daten übereinstimmen, also wenn das Granulat in den dafür vorgesehenen Container geplant ist. Gleiches gilt auch für die zehn gesicherten Stellplätze, von denen das Granulat aus einem Oktabin angesaugt wird.
Installation ohne Stillstandzeiten bei laufender Produktion
Da der Umbau während der laufenden Produktion ausgeführt werden sollte, wurden vor Ort die Trocknungsanlage auf der Bühne, Materialspeicher, vier »Navigatoren« sowie 6,3 Kilometer Förder- und Saugleitungen installiert. 84 Kleinstmengenabscheider vom Typ A2 wurden für die Spritzgießmaschine vorgesehen. Im gesamten Versorgungssystem sorgen Drehkolbenvakuumpumpen für ein gleichbleibendes Permanentvakuum zum Materialtransport. Die Pumpen arbeiten frequenzgeregelt, also bedarfsabhängig, was den Energieverbrauch senkt und den Verschleiß in der materialführenden Verrohrung mindert. Jede Pumpe wird von einem Zentralfilter Typ Sa3 vor Verunreinigungen in der Förderluft geschützt. Die Sicherheitsfilter reinigen die staubbeladene Luft von allen Fremdpartikeln, die größer als drei Mikrometer sind.
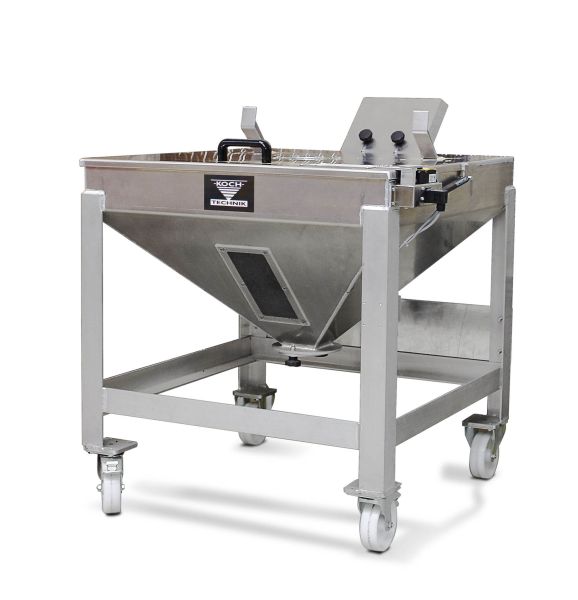
Die Materialcontainer, auch Sackaufgabebehälter genannt, öffnen
sich erst, wenn das einzufüllende Material zuvor über Barcode-Scanns verifiziert wurde. Bild: Koch-Technik
In der letzten Installationsphase wurden die Förderabscheider in der Spritzerei an die neuen Leitungen angeschlossen. Die neue Verrohrung hatten die Monteure von Koch zuvor oberhalb der Bestandverrohrung verlegt. »Die Förderabscheider konnten kontinuierlich im laufenden Betrieb direkt auf der Spritzgießmaschine getauscht werden. Jeder neue Abscheider ging sofort in Betrieb, sodass es keine Unterbrechung beim Wechseln gab«, erinnert sich Thorsten Köhler aus dem Bereich Moulding bei P&G Braun. Seitdem läuft die Anlage rund. Neben gestiegener Prozesssicherheit und unkomplizierter Materialverteilung ist die Kunststoffverarbeitung flexibler und energieeffizienter geworden. Erste Messungen nach einem halben Jahr mit der neuen Materialversorgung inklusive der Granulattrocknung wiesen 55 Prozent Energieeinsparung aus.