Neue Verfahren für anspruchsvolle Oberflächen
Maschinen und Anlagen für die Oberflächentechnik
Bei den Verfahren zur Herstellung von Kunststoffteilen mit qualitativ hochwertigen Oberflächen ist in den letzten Jahren viel in Bewegung geraten. Von der Serienfertigung folienhinterspritzter Bauteile über Komponenten mit Hochglanzoberflächen bis hin zu Oberflächen mit bestimmten Strukturen erstreckt sich heute die Bandbreite an Anwendungen. Dabei geht es nicht nur um Optik und Haptik, sondern auch um die gezielte Integration von Funktionalitäten. Bei der Realisierung von Anlagen zur Oberflächengestaltung ist anwendungstechnisches Wissen der beteiligten Partner gefragt.
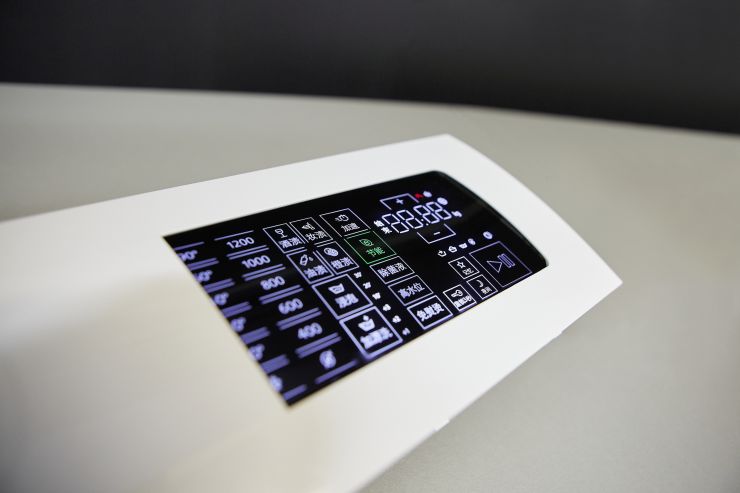
Ein Beispiel für das FIM-Verfahren ist die Produktion interaktiver, flexibler 3D-Displays für Waschmaschinen. Bild: Arburg
Grob lassen sich die Verfahren in drei Gruppen einteilen: verschiedene Folientechniken, Herstellung von Hochglanzoberflächen – bei Bedarf mithilfe variothermer Werkzeugtemperierung – und Abformen von Oberflächenstrukturen. Diese Verfahren sind in der Hauptsache werkzeugbasiert und können mit angepassten Spritzgießanlagen in der Großserienfertigung eingesetzt werden.
Bereiche, in denen die Folientechnik Anwendung findet, sind vor allem das Pkw-Interieur, mobile Elektronik und Weißware sowie die Medizin- und die Verpackungstechnik. Dabei sind die Anforderungen an die Bauteile besonders durch die Schwerpunkte funktionale Oberflächen und Dekoration definiert. Erforderlich für eine reibungslose Fertigung sind neben einer hochwertigen Maschinentechnik in sauberer Produktionsumgebung auch der wirtschaftliche Einsatz von Materialien und Verfahren, ein flexibler Herstellungsprozess mit der Integration vor- und nachgelagerter Fertigungsschritte sowie eine hohe Rückverfolgbarkeit und Reproduzierbarkeit. Neben Verfahren wie dem Film-Insert-Moulding (FIM) wird es zukünftig auch um eine vertiefte Automatisierung und Digitalisierung der Prozesse gehen.
Folientechniken
Mittels In-Mould-Decoration (IMD) lassen sich Design und Farben von einer Endlosfolie, die der Kavität automatisch zugeführt wird, auf die Bauteile übertragen. Die Folien werden von einer Rolle über eine Vorschubeinheit an der festen oder der beweglichen Platte des Schließsystems ins Werkzeug transportiert. So lassen sich große Losgrößen wirtschaftlich in Serie fertigen. Der Haupteinsatz von IMD findet sich in den Bereichen Automotive und Elektronik. Demgegenüber wird das In-Mould-Labelling (IML) zumeist in der Verpackungsbranche eingesetzt. Hier werden dünne Einlegefolien oder Labels automatisiert in die Kavitäten eingebracht und mit Kunststoff hinterspritzt. Die feste Verbindung zwischen Folie und Kunststoff erfolgt über den Einspritzvorgang. Durch Einsatz von Mehrfachwerkzeugen sowie gleichzeitiges Einlegen und Entnehmen lassen sich kurze Zykluszeiten erzielen. Die Teile sind ohne Nachbearbeitung verwendbar, eine nachgeschaltete Teileprüfung ist möglich.
Um Hinterspritzen handelt es sich auch beim Film-Insert-Moulding (FIM). In diesem Fall kommen vorgeformte Folien-Preforms zum Einsatz. Aufgrund von Partikelanlagerungen ist vor dem Einlegen eine Reinigung der Folien erforderlich. Dies kann über Bürsten oder ionisierte Luft erfolgen. Positioniert werden die Einleger meist über Vakuumgreifer, da hier das Aufnehmen an unkritischer Stelle erfolgen kann und der Greifer zum Werkzeug exakt positionierbar ist. Die Reinigung der Kavitäten läuft gleichzeitig zur Entnahme über Bürsten und ionisierte Luft. Arburg stellt in diesem Bereich technische Lösungen zur Verfügung, die sowohl an einen Reinraum angebunden als auch komplett in einen Reinraum integriert arbeiten können. Neben der Automobil- und Elektronikbranche ist auch die Medizintechnik ein wachsendes FIM-Segment. Damit lassen sich zum Beispiel interaktive Displays und intelligente Oberflächen fertigen. Solche Touchfolien kamen bislang vor allem auf ebenen Oberflächen zum Einsatz, sie lassen sich aber auch in 3D für gekrümmte Bauteile realisieren.
Ein gutes Beispiel für das FIM-Verfahren ist eine Anlage der Firma Hoefer & Sohn rund um einen hybriden »Allrounder 630 H« mit 2500 Kilonewton Schließkraft und Reinraummodul zur Produktion mehrerer Varianten interaktiver, flexibler 3D-Displays für Waschmaschinen. Die Teile entstehen in zwei Kavitäten. Die Folie ist elektrisch leitfähig und ermöglicht eine kostengünstige Herstellung. Die Spritzgießmaschine arbeitet angedockt an einen Reinraum, in dem alle vor- und nachgelagerten Schritte ablaufen, um elektrostatische Aufladung und Verschmutzung der Folien und Bauteile zu vermeiden. Das gesamte Handling erfolgt über einen Sechs-Achs-Roboter. Die Fertigteile werden nachgeordnet in verschiedenen Bearbeitungs-, Prüf- und Laserstationen kontrolliert. Je zwei vorbehandelte Folien werden in einem automatisierten Prozess mit den gespritzten Panels verbunden. In der Laserstation wird der Anguss abgetrennt, im Bedienbereich erfolgen die Finalisierung und optische Qualitätskontrolle der Touchpanels sowie die Verpackung für den Überseetransport.
Strukturierte Oberflächen
Die Serienfertigung von Spritzteilen mit strukturierten Oberflächen ist ein weiteres Verfahren, dessen Entwicklung maßgeblich durch die Automobilindustrie angeschoben wurde. Hier gibt es viele Möglichkeiten, Strukturen im Werkzeug anzulegen, die bis hin zu einer 3D-ähnlichen Anmutung reichen. Es geht um die gezielte Oberflächenmodifikation von Haptik und Optik, die Texturierungen mit 3D-Effekten, Leder- oder Carbon- und auch Hochglanzanmutungen kombiniert. Dabei ist die Gestaltung bezüglich der Bauteilgeometrie fast uneingeschränkt. Hinsichtlich der Werkzeugauslegung ist die Verwendung geeigneter Werkzeugstähle, die Zugänglichkeit der Kavitäten mit dem für die Strukturierung notwendigen Laser, der Materialabtrag sowie das Verhältnis von Narbtiefe zu Entformungsschrägen zu beachten. Alle Abgrenzungen müssen erhaben ausgeführt werden, die Strukturierungen sollten übergangslos in die Werkzeuggeometrie übergreifen. Arburg hat bereits die Umsetzung einiger Anwendungen in diesem Bereich begleitet.
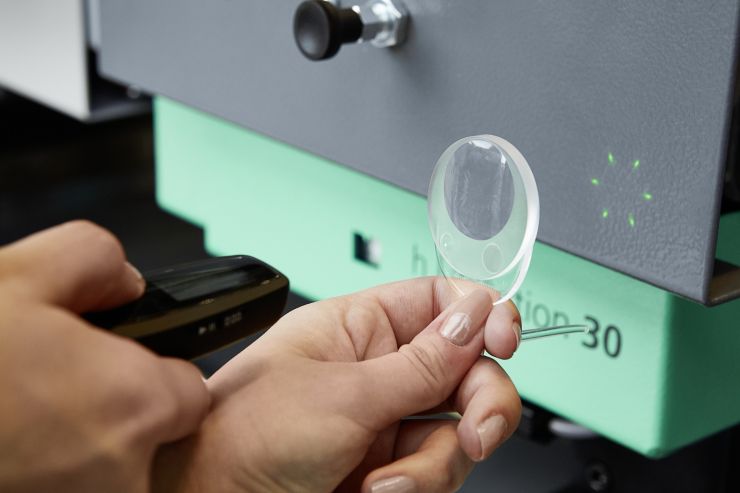
Ein hydraulischer »Allrounder 170 S« produziert in rund 50 Sekunden Zykluszeit strukturierte Optikplatten. Bild: Arburg
Um die Realisierung von Oberflächen mit optischer Funktionalität ging es zum Beispiel bei der Herstellung einer strukturierten Optikplatte. Auf einem hydraulischen »Allrounder 170 S« mit 180 Kilonewton Schließkraft wurden die Serienteile mit einem Gewicht von 7,5 Gramm in einer Zykluszeit von rund 50 Sekunden produziert. Zum Einsatz kam ein Einfachwerkzeug mit Einsatz der Firma Innolite. Die Strukturierung wurde mithilfe des Auswerferprägens auf die Optik aufgebracht, als Besonderheiten kamen eine Stickstoffspülung am Einzug sowie eine vorgelagerte Materialentstaubung zum Einsatz. Das Arburg-Assistenzpaket »4.production« standardisiert Sonderabläufe und macht komplexe Werkzeugtechnik rasch beherrschbar. Äußeres Anzeichen für die funktionierende Oberflächenstruktur der Teile waren verschiedene Anzeigenmuster, die je nach Lichteinfall auf eine Oberfläche projiziert werden konnten.
Dynamische Temperierung
Auch die Herstellung hochglänzender Oberflächen kam als Anforderung ursprünglich aus dem Automotive-Sektor. Um dies ohne die herkömmlichen, nachgeordnet ablaufenden und deshalb aufwendigen Verfahren wie Lackieren zu erreichen, setzt man hier eine dynamische Werkzeugtemperierung ein. Es liegt also nicht eine über weite Strecken konstante Werkzeugtemperatur im Prozess an, sondern das Werkzeug wird abwechselnd definiert beheizt und gekühlt. Damit lassen sich hochglänzende Oberflächen ohne weitere Bearbeitungsschritte und ohne sichtbare Bindenähte sowie mit geringerem Verzug herstellen. Über die »Allrounder«-Steuerungen lassen sich die Temperiergeräte direkt ansteuern, was den Komfort in der Produktion erhöht. Auf einem elektrischen »Allrounder 470 E Golden Electric«, ausgestattet mit einem Einfachwerkzeug und Robotersystem »Multilift Select«, wurde in einer Zykluszeit von 60 Sekunden eine hochglänzende Lichtblende für das Fahrzeuginterieur hergestellt. Die dynamische Werkzeugtemperierung erfolgte über ein Warm-Kaltwasser-Temperiergerät, das in die Ablaufsteuerung der Maschine integriert wurde.
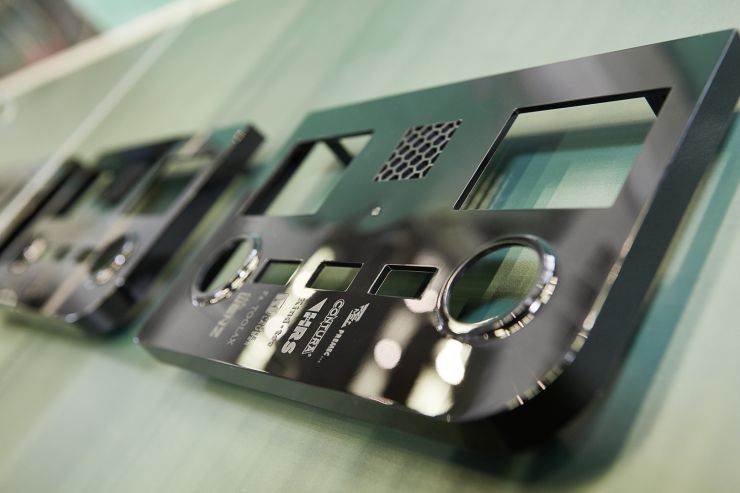
Eine elektrische Spritzgießmaschine fertigt mittels dynamischer Werkzeugtemperierung hochglänzende Lichtblenden aus PC/ABS. Bild: Arburg
Arburg unterstützt seine Kunden zusammen mit Systempartnern beim Aufbau individueller Produktions- und Turnkey-Lösungen zur Herstellung von Kunststoffteilen mit unterschiedlichen Oberflächenanforderungen. Die Palette reicht von der Verfahrenstechnik und Werkzeugauslegung – zum Beispiel mit den Themen Fixierung der Folien, Anspritzpunkte und Kavitätenanzahl, Realisierung von Werkzeugstrukturen oder Mehrkomponententechnik – über Maschinen und Automation bis hin zu Reinraumkonzepten, Prozesssteuerung und Datenbereitstellung.