Lösung für sehr große Rohre
Extruder
Mit zwei in den Nordosten Afrikas verkauften Extrusionsanlagen von battenfeld-cincinnati lassen sich sehr große Rohre mit einem Durchmesser von 2,7 Metern produzieren.
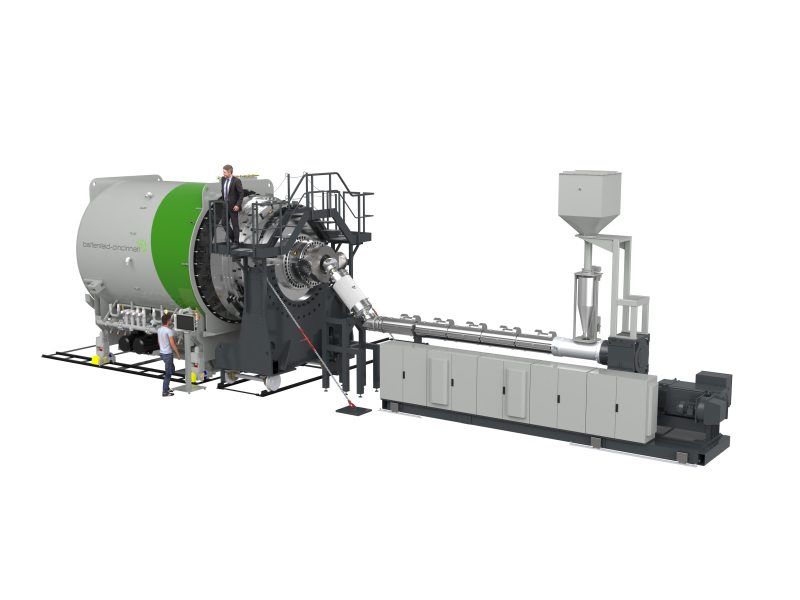
Mit diesem Rohrextruder lassen sich Kunststoffrohre bis 2,7 Meter Durchmesser fertigen (Bild: battenfeld-cincinnati).
Laut Unternehmensangabe handelt es sich dabei um die ersten Komplettanlagen, die derartig große Rohre in dieser hohen Qualität produzieren können. Für die Konzeption der Anlagen konnte der Extrusionsspezialist sowohl seine Gesamtanlagenkompetenz als auch die jahrzehntelange Erfahrung im Bau von Großrohranlagen nutzen. So trugen zum Projekterfolg die stetigen Optimierungsmaßnahmen zur Reduzierung von Sagging und damit zur Erhöhung der Rohrqualität sowie das maschinenbauliche Know-how bei, um Transport und Aufbau der großen Komponenten zu vereinfachen.
Der Kunde produziert auf den neuen Linien Großrohre mit einem Durchmesser von 2,7 Metern und bedient damit den steigenden Bedarf nach leistungsstarken Frisch- und Abwassersystemen. Kunststoffrohre spielen hier eine große Rolle, da sie sich aufgrund ihres geringeren Gewichts im Vergleich zu Betonrohren einfacher verlegen lassen, korrosions- und chemikalienbeständig sind und im Erdreich nicht durch Baumwurzeln beschädigt werden können.
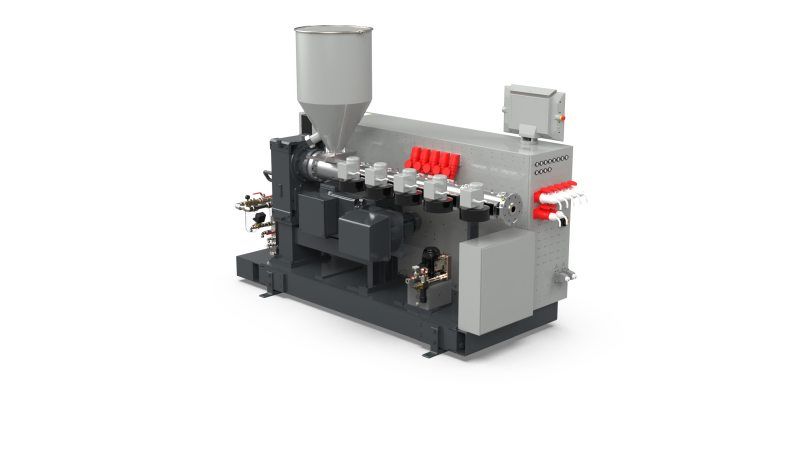
Der Extruder in Baugröße 45 rundet das Programm ab (Bild: battenfeld-cincinnati).
Für die Herstellung der Rohre in diesen Dimensionen sind zunächst leistungsstarke Extruder vonnöten, die die Schmelzemassen homogen plastifizieren können. Hier setzt battenfeld-cincinnati seit einigen Jahren auf die Baureihe »solEX NG«, die im Vergleich zu Vorgängerversionen laut Unternehmensangabe eine um bis zu 25 Prozent höhere Ausstoßleistung erreicht. Dank der verfahrenstechnischen Auslegung aus innengenutetem Zylinder und darauf abgestimmter Schnecken und Nutbuchsengeometrie arbeiten die Extruder mit einen reduzierten axialen Druckprofil, was für einen geringeren Verschleiß sorgt. Gleichzeitig garantieren hohe spezifische Ausstoßraten bei geringen Schneckendrehzahlen und um rund zehn Grad Celsius reduzierte Temperaturen eine effektive, aber schonende Schmelzeaufbereitung.
Eine weitere Verringerung der Temperatur um nochmals zehn Grad Celsius erreicht der statische Mischer »Optimelt«, der zwischen Extruder und Werkzeug installiert ist. Als Werkzeug selbst kommt ein Helix-Rohrkopf zum Einsatz, der mit seinem Zweistufenkonzept die optimierte Schmelzeverteilung bei geringem Druckaufbau übernimmt. Schließlich unterstützt die effektive Rohrinnenkühlung den stabilen Austritt der Schmelze aus dem Werkzeug. So sorgt die gesamte Einheit für minimierte Sagging-Effekte, was gerade bei Großrohren und ihrem hohen Gewicht von großer Wichtigkeit ist, um bestmögliche Wanddickenverteilungen ohne Ovalitäten zu garantieren.
Auch die Nachfolgeeinheiten sind auf die großen Dimensionen ausgelegt. Die Vakuum- und Sprühbäder arbeiten dabei ausschließlich mit frequenzgesteuerten Vakuumpumpen, die laut Hersteller rund 50 Prozent weniger Energie verbrauchen als herkömmliche Systeme. Ein geschlossener Wasserkreislauf im kompletten Kalibriersystem sorgt für einen Wasserverbrauch von nur einem Kubikmeter pro Stunde. Alle Nachfolgesegmente sind nur noch vier Meter lang, sodass sie einfach an den Bestimmungsort transportiert und dort lediglich zusammengefügt werden.
Abrundung nach unten
Die Extruder der Reihe »solEX NG« von battenfeld-cincinnati bieten hohe Ausstoßleistungen bei geringen Schneckendrehzahlen, effektive Aufschmelzleistungen bei niedrigen Schmelzetemperaturen sowie ein reduziertes Druckprofil und damit geringeren Maschinenverschleiß. Mit dem Modell »solEX NG 45« wurde die Baureihe nach unten abgerundet.
Wie die großen Modelle verfügt auch dieser Extruder über eine Verfahrenseinheit mit einem innengenuteten Zylinder und einer darauf abgestimmten Schneckengeometrie. Aus dieser Kombination ergeben sich laut Hersteller verfahrenstechnische Vorteile, die für eine hohe Qualität des extrudierten Halbzeugs sorgen. Bei der Verarbeitung von HDPE wird eine um rund 25 Prozent und bei PP sogar eine bis zu 40 Prozent höhere Ausstoßleistung versprochen. Der Energieverbrauch der Baureihe wird rund 15 Prozent geringer als bei der bisherigen »solEX«-Serie angegeben.