Gemeinschaftsprojekt LSR-Präzisionsspritzguss
Dosier-, Misch- und Förderanlagen
Zur Fakuma 2024 präsentierten der Dosier- und Werkzeugspezialist Elmet, der LSR-Hersteller Momentive und der Spritzgießmaschinenbauer Sumitomo (SHI) Demag ein Gemeinschaftsprojekt, bei dem die Beteiligten ihr spezielles Know-how rund um die Entwicklung, Herstellung und Verarbeitung von Flüssigsilikonkautschuk (LSR) eingebracht haben.
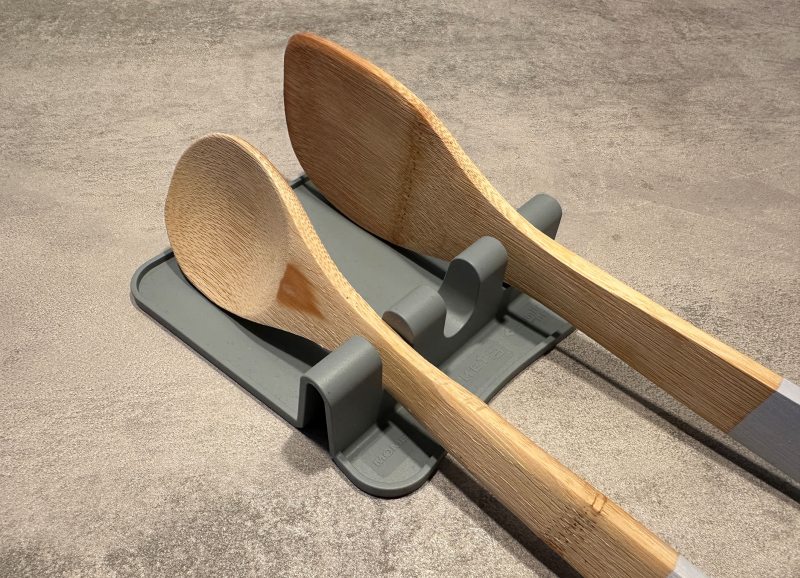
Anhand eines Löffelhalters präsentierten Elmet, Momentive und Sumitomo Demag ihr gemeinsames LSR-Know-how (Bild: Elmet).
Das Ergebnis dieser Zusammenarbeit ist der Löffelhalter »Drip Guard«, der verhindert, dass Tropfen während des Kochens unerwünscht auf der Arbeitsfläche gelangen, und der auch als Giveaway verteilt wurde.
Gleichbleibende Vulkanisation bei niedriger Temperatur
Das Formteil mit einem Schussgewicht von rund 55 g wird aus dem Zweikomponenten-Flüssigsilikonkautschuk »Silopren LSR 2670« von Momentive Performance Materials hergestellt. Das Material verfügt über niedrige Viskosität, hohe Reaktivität und gute mechanische Festigkeit. Aufgrund dieser Materialeigenschaften konnte sich das LSR-Material in vielen Anwendungen etablieren, auch für mechanisch hochbelastbare Teile in den Marktsegmenten Automotive, Elektrotechnik und Consumer Goods. Durch die angepasste Reaktivität ist es möglich, die Vulkanisationstemperatur um etwa 20 °C zu senken und trotzdem eine gleichbleibende Vulkanisation zu erzielen.
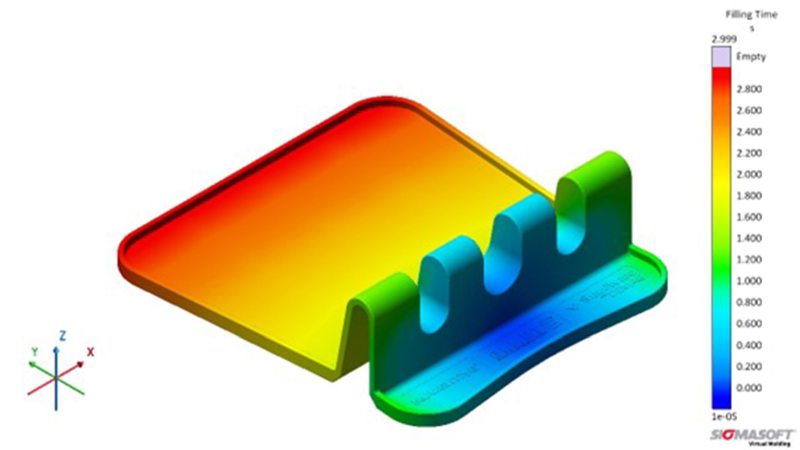
Momentive hat das Füllverhalten beim LSR-Spritzgießen des Drip Guard mithilfe von Simulationssoftware bereits im Vorfeld präzise bestimmt (Bild: Momentive).
Um die genauen Produktionsparameter bereits im Vorfeld bestmöglich zu bestimmen und zu optimieren, hat Momentive das Spritzgießverfahren mithilfe der Software »Sigmasoft Virtual Molding« von Sigma Engineering simuliert. Dabei wurden Füllstudien durchgeführt und bei angepassten Werkzeugtemperaturen die erforderlichen Vernetzungszeiten ermittelt, um das Produktionsverfahren zu optimieren. Zudem ermöglichen die neu ermittelten spezifischen Materialdaten der Flüssigsilikone von Momentive auch die präzise Vorhersage des zu erwartenden Schrumpfverhaltens der Formteile.
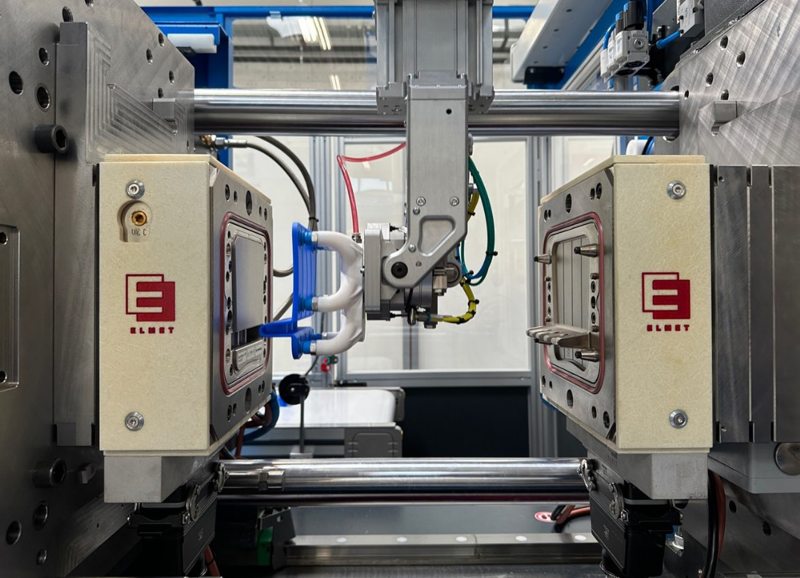
Bild: Elmet.
Bei Elmet lag die Verantwortung für die Idee, die Konstruktion und den Bau des Werkzeugs. Das Anspritzen erfolgt dabei über ein Nadelverschluss-Kaltkanalsystem »Smartshot P«. Bei diesem sorgt ein pneumatischer Antrieb für die präzise Bewegung der Düsennadel während des Einspritzens des Flüssigsilikonkautschuks in die Kavität. Zum exakten Balancieren des Füllvorgangs ist die Düse des »Smartshot«-Kaltkanalsystems kalibrierbar. Weitere Kennzeichen sind eine besonders lange Nadelführung und der 100-%-Schutz vor Verdrehungen der Nadel, deren Spitze ein Teil der formgebenden Kavitätskontur ist. Prinzipbedingt entfallen damit Produktionsabfälle wie Angusszapfen oder Angussverteiler vollständig.
Ebenfalls von Elmet stammt das Dosiersystem »Top 7000 Pro«, das für die präzise Einhaltung des Mischverhältnisses zwischen A- und B-Komponente und Additiven zuständig ist. Dank der speziellen Pumpeinheit ist die im System befindliche LSR-Menge besonders gering, was die Spülmenge bei Materialwechseln deutlich verringert. Sehr kostensparend wirkt sich aus, dass dank der optimierten Folgeplattengeometrie weniger als 0,4 % Restmenge im Fass verbleiben. Dieses wird vollautomatisch (ab Fassrand) gewechselt, was den Bedienkomfort erhöht und den Schulungsaufwand reduziert.
Die Fertigung erfolgte auf einer vollelektrischen Spritzgießmaschine »IntElect 130« von Sumitomo (SHI) Demag, die laut Hersteller im Vergleich zu hydraulischen Maschinen um bis zu 80 % effizienter ist. Ihre dynamischen Direktantriebe sorgen für sehr hohe Präzision. Große Holmabstände erhöhen die Flexibilität bei zugleich geringer Stellfläche.
Ergänzt durch das LSR-Maschinenpaket liefert SHI eine komplette Lösung für die Flüssigsilikonverarbeitung inklusive LSR-Spritzeinheit, Roboter, Vakuum, Heizung, Kühlung und Schnittstellen zur Peripherie. Die Messdaten aus dem Dosiersystem sind per OPC-UA direkt mit den Verarbeitungsdaten der Maschine verknüpft, sodass ein vollständig rückverfolgbarer und stabiler Produktionsprozess sichergestellt ist.