Verbundprojekt für energieeffiziente und nachhaltige Produktion von Kunststoffbauteilen
Werkstoff-, Verfahrens- und Methodenentwicklung
Das Bundesministerium für Wirtschaft und Klimaschutz fördert ein dreijähriges Forschungsprojekt zur Steigerung der Energie- und Ressourceneffizienz von Kunststoffverarbeitungs- und Recyclingprozessen.
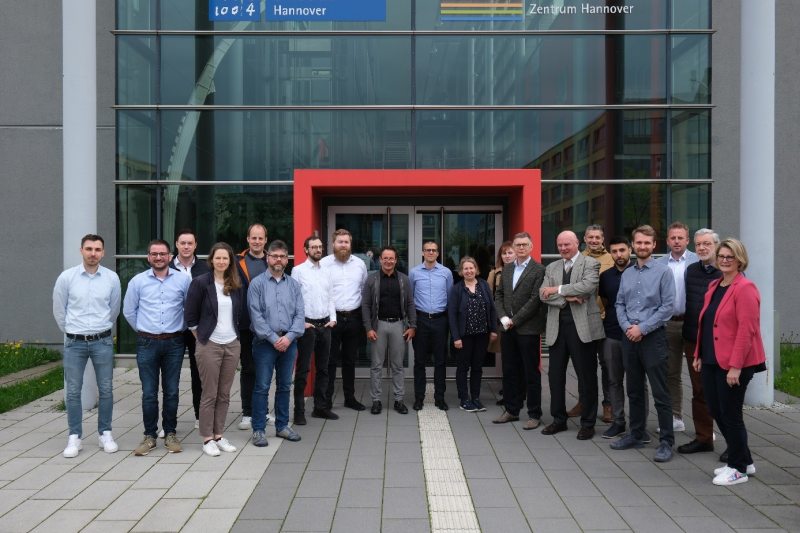
Bild: IKK Institut für Kunststoff- und Kreislauftechnik an der Leibniz Universität Hannover.
Infolge des Klimawandels sowie infolge steigender Energie- und Rohstoffpreise sind Energieeinsparungen und effiziente Ressourcennutzungen zu einem zentralen Thema vieler Branchen geworden. Auch für den Erhalt der internationalen Wettbewerbsfähigkeit ist die Steigerung der Energie- und Ressourceneffizienz notwendig.
An diesem Punkt setzt das Forschungsvorhaben »ENK – energieeffiziente und nachhaltige Produktion von Kunststoffbauteilen« an. Das Projekt wird im Rahmen des 7. Energieforschungsprogramms der Bundesregierung mit Mitteln des Bundesministeriums für Wirtschaft und Klimaschutz (BMWK) gefördert. Als Projektträger fungiert der Projektträger Jülich (PTJ). Insgesamt wird das Projekt laut IKK mit 2,57 Mio. Euro gefördert.
Das Projekt hat das Ziel, die Energieeffizienz in der Kunststoff verarbeitenden Industrie erheblich zu verbessern. Angesichts der aktuellen Debatten um Klimaschutz und steigende Energiekosten, die auch die Produktion von Kunststoffbauteilen betreffen, adressiert das Projekt eine der Hauptproblemstellungen der Branche, die über 2900 Betriebe und 320.000 Beschäftigte in Deutschland direkt betrifft.
Sechs Unternehmen im Projektkonsortium
Das Projektkonsortium besteht aus sechs Unternehmen sowie dem Forschungsinstitut IKK der Leibniz Universität Hannover und verfolgt das Ziel, insbesondere den Einsatz von elektrischer Energie in der Produktion von Kunststoffbauteilen um mindestens 30 % zu senken. Dies soll durch die Entwicklung hocheffizienter Werkzeugtechnologie für den Spritzguss und die Profilextrusion sowie durch Maschinentechnologie auf Basis von KI erreicht werden.
Ein auf Machine Learning basierendes Prozessüberwachungssystem zur Erkennung von vermeidbaren Energieaufwendungen soll in Kombination mit einer auf KI-basierenden Maschinensteuerung eine präzisere Kontrolle und damit eine erhebliche Reduzierung des Energieverbrauchs in den Kunststoffverarbeitungsprozessen ermöglichen Das System soll zunächst im Maschinenpark des IKK – Institut für Kunststoff und Kreislauftechnik – implementiert, erprobt und zur Herstellung eines Demonstrators genutzt werden, bevor es auf industrielle Verarbeitungsprozesse übertragen wird.
Auf der Ebene der Betriebsorganisation soll ein neuartiges Modell entwickelt und erprobt werden, welches Energie-, Nachhaltigkeits- und Wertschöpfungsaspekte entlang der Produktionskette abbildet und zur Identifizierung sowie Minimierung von Ineffizienzen und Energieverlusten genutzt werden kann. Die Nutzung von Rezyklaten sowie die Kombination der Verfahren Compoundieren und Spritzguss in einer Maschine gehören ebenfalls zu den Projektinhalten.
Der Fokus der Entwicklungsaufgaben im Projekt liegt auf den energieintensiven Prozessen Compoundierung, Profilextrusion und Spritzgießen. Ausgangspunkt der Entwicklung sind repräsentative Realprozesse aus der Industrie.
Durchgeführt wird das Verbundprojekt von den Partnern Konstruktionsbüro Hein GmbH, KraussMaffei Extrusion GmbH und KraussMaffei Technologies GmbH, iba AG, hankensbütteler kunststoffverarbeitung GmbH & Co. KG, Profex Kunststoffe GmbH, Grean GmbH, dem IKK sowie der Frötek-Kunststofftechnik GmbH als assoziierter Partner. Durch die gemeinsamen Anstrengungen aller Beteiligten wird eine nachhaltige Zukunft der Kunststoffverarbeitung angestrebt, die sowohl dem Klimaschutz als auch der Kosteneffizienz dient.