Optimierung von Formoberflächen
Verfahren
Durch eine neue Oberflächenbehandlung der H-O-T Härte- und Oberflächtentechnik GmbH & Co. KG können Formoberflächen geschützt, die Verschleißbeständigkeit erhöht und somit Zeit und Geld durch nachbearbeitungsbedingte Produktionsausfälle gespart werden.
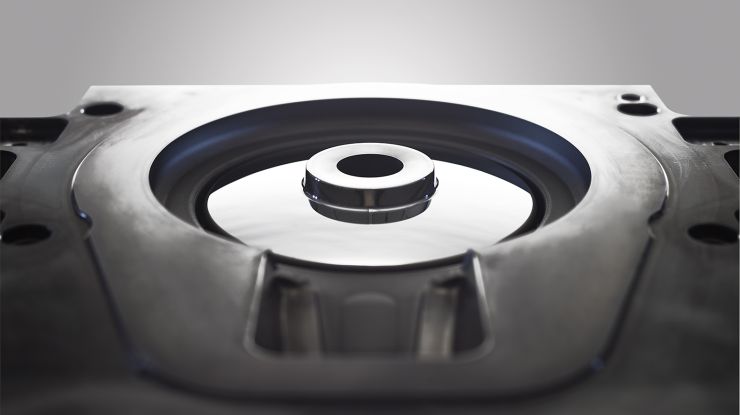
Beispiel für eine Spritzgussform, die bei H-O-T mit der »hi-Fusion«-Beschichtung veredelt wurde. Bild: H-O-T
Die Verarbeitung von Kunststoffen mittels Spritzgießen ist aus dem täglichen Leben nicht mehr wegzudenken. Die Flexibilität des Verfahrens, von der Fertigung einfachster Formteile bis hin zu Präzisionsteilen mit höchsten Anforderungen, machen den Spritzguss zu dem am weitest verbreiteten Verfahren zur Herstellung von Kunststoff-Massenteilen. Die höchsten Kosten entfallen bei dieser Fertigungsvariante im Normalfall auf das formgebende Werkzeug, das häufig komplexe Geometrien aufweist, gepaart mit polierten oder strukturierten Oberflächen für Sichtteile oder für Teile mit erhöhten Anforderungen an die Haptik. Um wirtschaftlich produzieren zu können, sind Schusszahlen im Bereich von mehreren Tausend, je nach Formteil sogar Millionen notwendig.
Mit steigenden Anforderungen an die Formteile und der damit einhergehenden Verwendung von Füllstoffen wie Glas- oder Kohlefasern steigt die abrasive Wirkung der zu verarbeitenden Kunststoffmasse, was wiederum zu einem erhöhten, ungewollten Werkzeugverschleiß führen kann. Um dieser Problematik zu begegnen, werden Formen aus vorvergütetem oder gehärtetem Stahl eingesetzt, bei besonderen Härtefällen wird auf verschiedene Nitrier- und Beschichtungsverfahren zurückgegriffen. Doch auch diesen Lösungen sind Grenzen gesetzt. So führt das Nitrieren häufig zu Problemen bei hochglanzpolierten Formen, bei beschichteten Werkzeugen sind selbst kleinere Reparaturen an der Form mit einem aufwendigen Entschichten, Nacharbeiten und erneutem Beschichten verbunden. Die Firma H-O-T bietet als Lösung für diese Probleme das neue »hi-Fusion«-Verfahren an, wobei der Fokus vor allem auf der Verbesserung der Verschleißbeständigkeit und Kratzfestigkeit der Formoberfläche liegt.
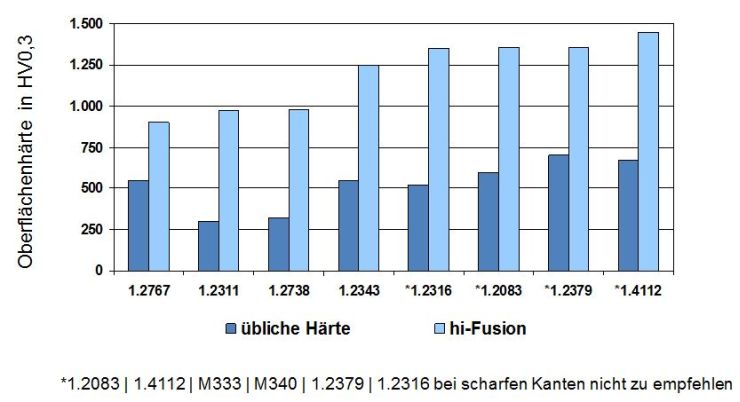
Oberflächenhärte vor und nach der Behandlung, gemessen bei H-O-T. Grafik: H-O-T
Bei dieser neuen Behandlung handelt es sich um ein Niedertemperatur-Diffusionsverfahren, bei dem Fremdelemente bei einer Temperatur von circa 400 Grad Celsius in die Stahloberfläche eindiffundieren. Das Spendermedium innerhalb der Anlage liegt hierbei im gasförmigen Zustand vor.
Eindeutige Vorteile
Das Verfahren besitzt eine Vielzahl an Vorteilen: Im Gegensatz zu den Nitrierverfahren baut es keine Verbindungsschicht auf, wodurch – eine beschichtungsgerechte Vorbehandlung vorausgesetzt – keinerlei Maßänderung zu erwarten ist. Die Neigung zum Abplatzen von scharfen Kanten, die vor allem beim Nitrieren von hochlegierten Materialien häufig auftritt, ist bei dem neuen Beschichtungsverfahren nicht gegeben. Die Härte des Grundwerkstoffs wird, im Gegensatz zum vergüteten beziehungsweise gehärteten Zustand, deutlich erhöht. Materialabhängig werden Härtewerte von bis zu 1400 HV0,3 erreicht.
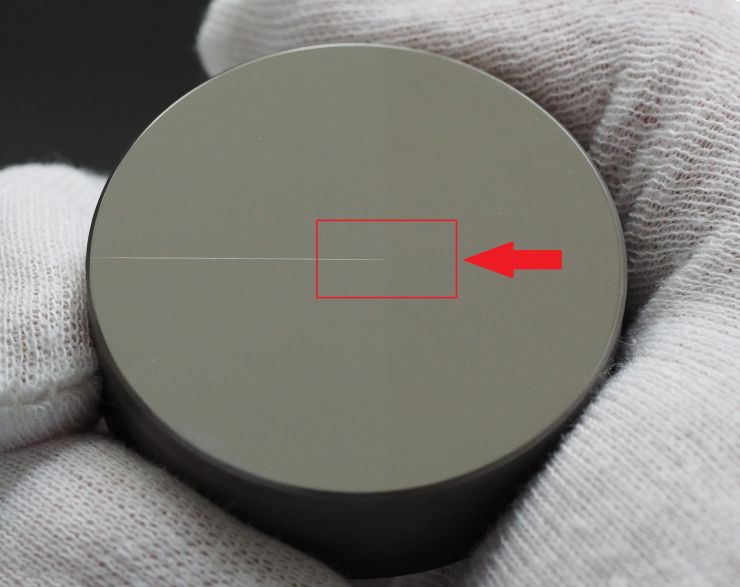
Kratzprobe, linke Seite unbeschichtet, rechte Seite mit dem neuen Verfahren behandelt. Bild: H-O-T
Die Polierfähigkeit der Oberfläche ist selbst im beschichteten Zustand noch besonders hoch, Mikrorisse und Poren werden durch Druckeigenspannungen, die bei der Einlagerung der diffundierenden Elemente entstehen, geschlossen. Kleinere Beschädigungen können aufgrund der Eindringtiefe von 40 bis 80 Mikrometern durch Polieren egalisiert werden. Zudem kann der Glanzgrad sogar nach dem Beschichten noch eingestellt werden, ohne die Beschichtung selbst zu beeinträchtigen oder die Verschleißbeständigkeit zu reduzieren. Bei schweren Beschädigungen ist häufig eine Reparaturschweißung erforderlich. Diese ist auch in den beschichteten Bereichen möglich, durch eine erneute »hi-Fusion«-Behandlung ist eine Anpassung der Verschleißbeständigkeit selbst auf den geschweißten Flächen möglich. Die Instandhaltungskosten für Spritzgusswerkzeuge werden durch diese Vorteile deutlich reduziert und die Werkzeuglebensdauer wird erhöht. Einen weiteren, positiven Effekt des Verfahrens stellt die verbesserte Korrosionsbeständigkeit des verwendeten Stahls im Gegensatz zum unbeschichteten Zustand dar. Dies konnte durch verschiedene Versuche mit wechselnder Korrosionsbelastung und Salzsprühnebeltests belegt werden.
Für besonders hohe Anforderungen ist es möglich, ein Schichtsystem aus der neuen Diffusionsbeschichtung und einer an den Anwendungsfall angepassten PVD-Beschichtung aufzubauen. Die »hi-Fusion«-Beschichtung dient hier als Stützschicht für die nur wenige Mikrometer dünne PVD-Schicht und gleicht etwaige Schwächen des Grundmaterials aus, wodurch Schichtausbrüche (Eierschaleneffekt) vermieden werden. Bei schwerwiegenden Problemen mit Anhaftungen wurden beispielsweise Systeme aus einer »hi-Fusion«-Beschichtung und einer darüber liegenden Cr2N-Beschichtung realisiert.
Anforderungen im Vorfeld
Um eine einwandfreie Behandlung zu gewährleisten, muss das Werkzeug bereits im Vorfeld von möglichst allen Verunreinigungen befreit werden. Hierzu zählen flüssige Medien wie Kühl- und Schmierstoffe, aber auch Korrosionsschutzöle, Späne, Kunststoffanhaftungen und Verunreinigungen der Kühlbohrungen. Rückstände, die sich während der Behandlung noch auf der Oberfläche befinden, hindern die Adsorption beziehungsweise Absorption des Behandlungsmediums und führen dazu, dass die Beschichtung in diesen Teilbereichen nicht eingebracht werden kann.
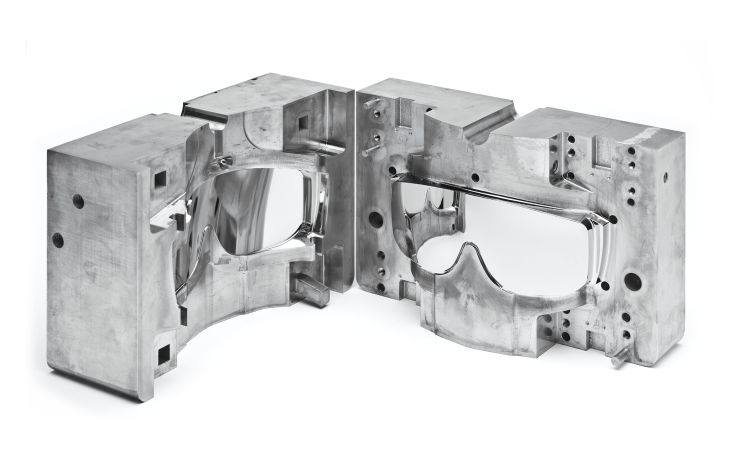
Beide Hälften eines behandelten Form-einsatzes, die Funktionsfläche wurde mit dem neuen Verfahren beschichtet und poliert. Bild: H-O-T
Da das Verfahren im Unterdruck durchgeführt wird, müssen Werkzeuge zerlegt und die Kühlbohrungen frei von Verunreinigungen sein, da es selbst bei den geringen Behandlungstemperaturen zum Abdampfen von Rückständen kommen kann, die sich dann auf der Bauteiloberfläche und der Kontur niederschlagen können. Bei der Verwendung von gehärtetem Stahl ist zu beachten, die Zielhärte und somit die Anlasstemperatur so zu wählen, dass bei der Behandlungstemperatur des Verfahrens keine Härteverluste zu erwarten sind.
Es können alle Stähle behandelt werden, die bei der Verarbeitung von Kunststoffen Verwendung finden, von vergüteten Kunststoffformenstählen (zum Beispiel 1.2312, 1.2738) über Warmarbeitsstähle (zum Beispiel 1.2343, 1.2344) bis hin zu korrosionsbeständigen Formenstählen (1.2083, 1.2316).
Realisierte Projekte
Die Firma H-O-T konnte in den vergangenen Jahren in Kooperation mit namhaften Kunden aus dem Bereich Formenbau bereits viele Projekte verwirklichen. Die beschichteten Werkzeuge finden ihre Anwendung beispielsweise in der Elektrotechnik, Automobilen, Haushaltsgeräten, der Verpackungsindustrie, Medizintechnik und der Spielwarenindustrie. Hierbei wurden Werkzeuge mit Einzelstückgewichten bis über zwei Tonnen innerhalb kürzester Zeit gereinigt sowie für das Verfahren vorbereitet und behandelt. Die positiven Rückmeldungen der Anwender zum Verhalten der beschichteten Werkzeuge im Einsatz belegen die Vorteile des neuen Verfahrens.